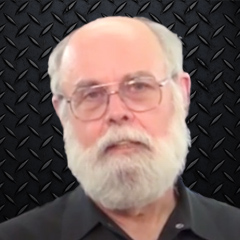
Understanding Cam Specs: Part 2
Bruce TessmerDescription
Lift
The first of the big three is lift. Lift is defined as how far the valve moves off of the valve seat, or in other words how far the valve opens. The distance that the cam moves the tappet and pushrod is known as cam lift or tappet lift. It’s the difference between the radius of the base circle and the distance from the centerline of the camshaft to the nose of the cam lobe.
The pushrod pushes one end of the rocker arm and forces it upward. The rocker arm is nothing more than a lever. The valve side that pushes down on the valve stem is longer than the pushrod side. The valve side of the rocker arm actually pushes the valve down farther than the cam pushes the pushrod end up. The ratio of the length of the valve side and the pushrod side of the rocker arm is called the rocker ratio. If you multiply the cam lift by the rocker ratio, you’ll get the theoretical valve lift.
Lift is important because opening the valve further allows air or exhaust to flow in or out more quickly. You get a better cylinder fill and more efficient elimination of exhaust gases.
If you plan on running stock valve springs in your engine, you need to select a camshaft that does not exceed the maximum lift of your springs. These are called bolt in cams. A true bolt in cam does not require any modifications or other components for installation. Stock tappets, pushrods, rocker arms, and valve springs can be reused. Cam timing is also appropriate for a stock engine.
Using stock valve springs is perfectly OK for most street applications. But, in addition to the limitations on lift, you can’t exceed the stock rev limit. If you plan on operating the engine and at higher rpm, you should install a set of performance valve springs.
When a higher lift cam is installed, the valve may no longer be the most restrictive part of the system. The air cleaner, carb, throttle body, intake port, exhaust port, and the exhaust system also play a part in restricting the airflow. A performance high flow air cleaner assembly, and a performance high flow exhaust system are necessary to help move air quickly and efficiently through the engine. Performance air cleaner and exhaust help the cam to reach its full potential. A larger carburetor or induction module can also be helpful or necessary.
Duration & Intake Closing Time
Two important valve timing events are the valve opening & the valve closing times.
Intake closing time and duration are two very closely related events, so it is important to look at them together. Intake closing time is related to duration because it actually plays a part in determining duration. Closing the intake valve later in the cycle increases duration.
A cam with a longer intake duration will have a later intake closing time. Duration is defined as the number of degrees of crankshaft rotation that a valve is open. It’s determined by the point when the intake valve opens and the point when it closes. The earlier it opens and the later closes, the greater the duration. The later it opens and the earlier it closes, the shorter the duration.
There are horsepower cams with lots of duration & late intake closing time, and there are torque cams with shorter duration and earlier intake closing time. Torque cams and horsepower cams are actually two ends of the camshaft spectrum and specialize in making either horsepower or torque, but not both.
A cam that falls in the middle of the spectrum, sometimes called a mid range cam, may suit you better. Duration and intake closing times are somewhat more than stock, but they’re not extreme. There is an increase in horsepower but low-end torque is generally increased as well. Mid range cams will not provide as much of an increase in torque or horsepower as the specialty cams, but they provide a general increase in performance across the rpm range.
After watching this video, you will have a good grasp on what to look for when choosing a cam. If you are looking for low-end torque or a dependable mid-range cam, you will see that bigger is not always better. If you want to go big, you will also need a big budget and then, hold on tight!
If you missed Understanding Cam Specs: Part 1, be sure to watch that video as well for a comprehensive understanding of cam specs.
Next, watch Understanding Cam Specs: Part 3 here.
Still hungry for more? Check out these other upgrade projects from Fix My Hog:
Cam Upgrade and Tensioner Upgrade
Cam Upgrade and Gear Driven Cam
M8 Cam Upgrade
Thank you to S&S Cycle for sharing this video series with Fix My Hog.
Hi, Bruce, here from S&S Cycle. Welcome to our second video on understanding cam specifications. In our first video, we showed you how a four stroke gasoline engine works and detailed the role of the valve train in the process. The valve train of course is controlled by the cam shaft. If you haven't seen the first video, I'd highly recommend that you watch it before you view this one.
We call this video The Big Three because we'll be explaining the three most important specifications to consider when selecting a cam shaft for your engine. They are lift, duration and intake closing time. It's not uncommon for riders to look at a chart of cam specifications and just choose the cam with the biggest numbers. Bigger is better, right? Chances are with that approach.
You'll spend a lot of money but you won't be very happy with the results. After all, if it was that easy we could just make one big nasty cam and call her the day. In reality, we make a range of cams for a range of applications. The cam you choose has to be right for your engine. And just as importantly for your riding style.
So let's get down to business and look at the first of the big three, which is lift. Lift is defined, as how far the valve moves off the valve seat. Or in other words, how far the valve opens. This illustration shows a profile of a cam shaft. As I mentioned in the first video, as the cam shaft turns the load pushes the tap it up.
The tap it moves the push right upward, which moves the rocker arm. And the rocker arm opens the valve. As the cam turns and the nose of the cam passes the tappet roller, valve spring pressure pushes the valve to the closed position, which pushes the rocker arm push rod and tap it downward, keeping the tap it in contact with the candle a bit all times. The distance that the cam moves to tap it and push her out is known as cam lift or tap it lift. It's the difference between the radius of the base circle and the distance from the center line of the camshaft to the nose of the cam lobe.
This is called cam lift or tap it lift. When we're designing a cam and we want to increase the lift. There are two ways of doing it. We could increase the height of the lobe which will push the tap at farther or we could decrease the size of the base circle which will increase the cam lift by increasing the difference between the radius of the circle and the height of the lobe. In fact, that's what engine builders in the early days of hot riding actually did.
They would grind the heel of the cam smaller to get more lift from a stock camshaft. Crude, but effective. Okay. We've got cam lift figured out but what about valve lift? The push rod pushes, hence the name one end of the rocker arm and forces it upward.
The rocker arm is nothing more than a lever. And the valve side that pushes down on the valve stem is longer than the push rod side. So the valve side of the rocker arm actually pushes the valve down farther than the cam pushes the push rod end up. The ratio of the length of the valve side. And the push rod side of the rocker arm is called the rocker ratio.
So if you multiply the cam lift by the rocker ratio you'll get the theoretical valve lift. Why theoretical? Well in the real world the push rods and rocker arms, both flex under stress and you will lose a small amount of the theoretical lift. This is especially true with high-lift cams and heavy performance valve springs. Because the increased spring force and the valve train will increase the flexing.
Another factor is that at high RPM, the acceleration of the valve train components is much higher and adds even more stress to these parts. That's why S&S sale super-strong chromoly steel push rods and high-strength forge rocker arms to minimize the flexing and increase valve timing accuracy. The rocker ratio for all Harley-Davidson Evolution, twin cam 88 ,96 and 103 engines is 1.625:1. The rocker ratio for Milwaukee-Eight engines is 1.6:1. So you get over one and a half times more lift at the valve than at the cam.
Sweet. Why is Lyft important? Opening the valve farther allows air or exhaust to flow in or out more quickly. You'll get a better cylinder fill and more efficient elimination of exhaust gases. It'll be pretty easy to demonstrate this idea in the kitchen sink.
When I opened the valve on this faucet, water comes out. If I open it farther, water comes out faster. That's pretty intuitive. And the same principle applies to the valves in an engine. Open the valve in the cylinder head farther and the air can flow into and out of the cylinder faster because the valve presents less restriction to flow.
We're most concerned about the intake valve. Since we only have atmospheric pressure to force the air into the cylinder, the exhaust valve is important but exhaust gases are forced out of the cylinder by the piston, which can exert much greater pressure. It's no coincidence that the intake valve is almost always larger than the exhaust valve. Right about now you may be thinking, yeah, give me some lift, give me the highest lift cam they make. Not to be too much of a buzzkill but lift does have its limits and lift does have some downsides.
First of all, just as there's a limit to how far I can open this faucet, there are physical limits on how far a valve in your engine can be opened. One of the factors limiting valve lift in your engine is the valve spring pack. It's probably easiest to demonstrate with this spring tester, as the opens the valve the valve spring is compressed and exerts an opposing force which closes the valve again when the cam allows it to close. There is a limit to how far a spring can be compressed. Beyond that limit.
The coils of the spring will contact each other and bind up. It's not too surprising that this condition is called coil bind. Coil bind is pretty extreme. It's the worst case scenario. Things break when this happens.
The cam is trying to compress the spring that can't be compressed anymore. And something's got to give. A less apparent problem of higher lift is the fact that valve springs will fail due to metal fatigue if operated at valve lifts higher than they were designed for. Even if coil binding doesn't occur. Here's another spring pack issue with high lift.
We also need to make sure that the top valve spring collar doesn't come down far enough to contact the top of the valve seal. You can see when the valve opens farther the top collar comes closer to the valve guidance seal. We have to make sure that these parts don't touch. So if you plan on running stock valve springs in your engine, you need to select a camshaft that does not exceed the maximum lift of your springs. These are called Bolt-in cams.
A true Bolt-in camp does not require any modifications or other components for installation. Stock tablets, push rods, rocker arms and valve springs can be reused. Cam timing is also appropriate for a stock engine. Using stock valve springs is perfectly okay for most street applications, but in addition to the limitations on lift you can't exceed the stock rev limit. If you plan on operating the engine at a higher RPM you should install a set of performance valve springs.
In addition to align the use of higher lift cam grinds performance valve springs apply more force and close the valve more quickly, ensuring that the valve follows the profile of the cam lobe and closes fully at higher RPM. Maximum lift for Bolt-in cams, depend mostly on the stock valve springs in the engine. Valve springs and stock Harley Davidson Evolution and 1999 to 2004 twin cam 88 engines can accept cams up to about 515,000 lift. 2005 and later twin cam, 88,96 and 103 engines can run cams of up to five 85 lifts with stocks springs. Milwaukee-Eight engines can handle lifts up to 475 lifts with stock valve springs.
How comes the M* can't handle as much lift? Well with four valves per cylinder, you don't need as much lift to get more air into the cylinder installing a Bolt-in cam and then using the stock valve springs can be a pretty economical upgrade. However, if you decide to install a set of high-performance valve springs, be aware that there will be some added expense because not only will you be buying some springs, you're also going to remove the cylinder heads to install it. So labor costs are increased. Okay.
We've increased the lift of our valves and increase the flow but now we need to be able to supply air to the valve fast enough to take advantage of that increased flow. When a higher lift cams installed, the valve may no longer be the most restrictive part of the system the air cleaner carb or throttle body, intake port, exhaust port, and the exhaust system also play a part in restricting the flow. That's why we consider a performance high flow air cleaner and performance exhaust to be a prerequisite anytime a performance cam is installed. They're easy to install yet they yield significant increases in performance and help the camshaft to achieve its full potential. Depending on the size of the engine a bigger car with throttle body might also be in order.
Another way to make the most of a high lift can is to have the cylinder heads pointed to increase the amount of air the intake ports can deliver. And the amount of exhaust the exhaust parts can expel. Since all the valve train parts are moving farther with a higher lift cam that components have to accelerate more quickly and move faster, resulting in more stress on the parts accelerated where an increased valve train noise. This is generally not a problem with both in cams but can certainly be an issue with very high lift cams. Really high lift cams may also exceed the designed geometry of the stock rocker arms and exert a lot of side thrust on the valves at maximum lift.
For any cam shaft over 585 lift, we recommend that the stock rocker arms be replaced with roller rockers. The roller on the rocker arm kit reduces valve tip wear as well as side thrusting on the valve stem. However, the additional cost of a set of roller rocker arms may be a factor in deciding between a Bolt-in cam or a high-lift cam. There are applications we're going for maximum possible lift. Isn't the best idea.
For example when we were developing our 551 touring camp set we could have designed it with a 585 lift and still it would bolt into a stock engine. But since this cam was intended for touring applications which is all about going the distance we opted for a slightly lower 550 lift. The goal was to reduce valve train noise and to improve valve train life. Nailed it both times. It may seem like I'm trying to talk people out of using high lift cams, but that's not the case.
However, you should be aware of the downside as well as the possible gains. Luckily, lift is not the only tool we have to increase performance. So let's move on to the all-important subject of valve timing. Two valve timing events that we'll be mostly concerned with will be valve opening and closing times. S&S and the majority of the industry considered the valve to be open or closed when the tap it is 53000 from its lowest point of travel, or to put it in another way off the base circle of the cam.
According to historical urban legend that's there was enough flex or deflection in the early push rod valve trains, that it took as much as 53000 of tappet lift before the valve would actually start to move an opening. And the valve could actually be closed 53000 before the tap it was on the base circle of the cam. We're not entirely sure that's true but it makes a great story. Not all manufacturers use the 53,000 measurement. You may see opening and closing time specified at 50,000 or even 20,000.
Automotive camp timing events are sometimes specified at as little as 5000 tappet lift. So if you're comparing cam specs from different manufacturers be sure you know how they're arriving at their numbers. Now that we have a handle on valve opening and closing times let's look at the other two big three specifications. Intake closing time and intake duration. These are two very closely related events.
So we really need to look at them together. Let's start with intake closing time spec. Intake closing time is related to duration because it actually plays a part in determining duration. Closing the intake valve later in the cycle increases duration. In general, a cam with a longer intake duration we'll have a later intake closing time.
But not always, as we will see. Duration is defined as the number of degrees of crank shaft rotation that a valve is open. It's determined by the point when the intake valve opens and the point when it closes. The earlier it opens and the later it closes the greater the duration. Conversely, the later it opens and the earlier it closes the shorter the duration.
As I mentioned earlier in the first video duration is not measured in time but in degrees of crank shaft rotation. So what is the effect of duration? So let's go back to the sink for an illustration. If I open the valve, some water comes out. If I leave the valve open longer, I get more water.
If some is good, more is better, right? That kind of thinking will almost always get you in trouble. It maybe true up to a point. But that point depends on the engine and the application. Now that we've defined intake closing time and duration We can talk about how they affect performance.
Let's take a look at this example the piston is just about the top dead center on the exhaust stroke. Exhaust stroke? Aren't we talking about intake timing? We are in indeed talking about intake timing but it starts at the end of the exhaust stroke. You'll notice that the intake valve is already starting to open.
During this part of the cycle, the intake and exhaust valves are both open. This is called overlap. Why are both intake and exhaust valve to open? Intuitively, it may seem like this would be a bad thing. Here's why it's not.
First we have to remember that this all happens very quickly. If you're putting down the road at 2,500 RPM that piston is going up and down almost 42 times a second and we need to start the opening process in time to have the greatest lift occur at the most advantageous time. The other thing to realize is that when the engine is running, it isn't just the piston sucking air into the cylinder and pushing exhaust out. We also need to understand the role of the air and exhaust gases moving in and out of the engine at high velocity. Factor the overlap condition.
This begins towards the end of the exhaust stroke. And by this point, the exhaust gases are moving very fast out of the exhaust port and out of the exhaust pipe. Here's where mass and velocity also known as inertia come into play. The exhaust gases have mass, and since they are moving out of the exhaust pipe they also have velocity. And like any matter in motion the exhaust gases book continue to flow in the direction they're moving until something stops them in accordance with Newton's first law of motion.
Eventually the burn gasses in the chamber will be exhausted but the gases in the exhaust pipe keep riding on moving out the pipe. It would be rude to say the pipe suck but the exhaust gas is rushing out of the exhaust pipe do create a vacuum in the combustion chamber. And since the intake valve has just opened that vacuum starts to draw fuel and air into the combustion chamber before the intake stroke even starts. Stock camshafts will have very little or even no overlap to reduce hydrocarbon emissions. The lack of overlap reduces the possibility of any unburned gasoline in the new charge being drawn all the way through the combustion chamber and out the exhaust pipe by the escaping exhaust gases.
But this then reaches top dead center and starts down the cylinder on the intake stroke. The exhaust valve closes and the vacuum created by the moving piston continues to draw air and fuel into the cylinder. The piston passes bottom dead center or BDC and starts to move back up in the cylinder. Notice that the intake valve is still open. How come?
The piston is going up so it can't still be drawing air into the cylinder. Common sense would suggest that the piston should be pushing the air back out. Again we need to realize that in a running engine this all happens very fast. The fact is that even though the piston has reversed direction, when the engine is at speed air is still flowing into the cylinder. Not so much of at high-low starting but certainly at higher RPm.
How does that work? Again, air is composed of matter and it has mass. So if you get it moving in a certain direction like into your intake port, inertia will keep it moving in that direction until something stops it. Be assured that something will eventually stop it. But for a little while that air continues to flow into the cylinder, giving us additional cylinder fill.
Bonus, more air, more power. it's standard to reason that the faster the engine is turning the faster the air will be moving in the intake track. So the harder the air will be disturbed and the longer it will continue to flow. So you can continue to fill the cylinder for a longer time. As long as the intake valve is still open.
So if your goal is to increase higher RPM horsepower a cam with later intake closing time is the way to go. For a motor that will be run at lower RPM not so much. A long duration camshaft with the late intake closing time is best suited for larger engines with higher compression ratios that are intended to make peak horsepower at higher RPM. Long duration cams will normally also have an earlier intake opening time and take advantage of the vacuum that the exhaust system creates in the combustion chamber to increase cylinder fill. A drag race engine would be a good application for a long duration camshaft.
A drag racer wants high RPM horsepower to produce the highest tops speed. But wait a minute you say, isn't racing all about acceleration? Isn't torque what you need? the answer to that is yes. You do need to arch to accelerate, but in drag racing we aren't concerned with low or mid range torque since drag engines aren't operated at low RPM.
A drag racer comes out of the hole as hard as he or she can and never lets off until the finish line. Another reason that long duration cams work well in high compression engines is that they make those engines easier to turn over for starting. A high compression engine develops a lot of pressure in the combustion chamber when the intake charge is compressed. That high combustion chamber pressure makes the engine harder to turn over during starting. At starting RPM, which is pretty low.
The intake charge does not have much velocity and it's easily stopped. If the intake valve closes later in the compression stroke some air may actually be pushed out of the intake valve during starting. That bleeds off some of the air in the cylinder before the intake valve closes, reducing the amount of air that will actually be trapped in the cylinder during the compression stroke. So the engine turns over easier. Here's a potential pitfall if you select a cam shaft, based on the biggest numbers.
What happens when a long duration cam is installed in a low compression engine? Just like with the high compression engine, air will be bled off reducing cylinder pressure, but since a low compression engine doesn't have much cylinder pressure to begin with. The result will be very low cylinder pressure at starting RPM. If the cylinder pressure is low enough the engine may not even start but it'll certainly turn over easily. This is one reason that choosing a cam just because it has the biggest numbers is not a good idea.
This is sometimes called over camming an engine. Once started an over cam engine will be sluggish at low RPM because of the low combustion chamber pressure. Your bike will be a pooch off the line. At really high RPM it may run pretty well, but the low and middle range where you spend the most of your time riding are going to be weak. Lower compression engines work best with shorter duration cams with earlier intake closing times.
A low compression engine where the short cam generally tends to produce ample torque at lower RPM. The trade-off is the engine will not make as much high RPM horsepower. A good application for short duration cams would be a touring bike. If you need to accelerate a heavy bike up to freeway speed pass a semi, or pull a trailer up a hill. You need low and mid-range torque.
So we have horsepower cams with lots of duration late intake closing time. And we have torque cams with shorter duration and earlier intake closing time. Torque cams and horsepower cams are actually two ends of the camshaft spectrum. And specialize in making either horsepower or torque, but not both. If you want some more of everything a cam that falls in the middle of the spectrum sometimes called the mid range cam may suit you better.
Duration and intake closing times are somewhat more than stock. But they're not extreme. There is an increase in horsepower but low end torque is generally increased as well. Mid range cams will not provide as much of an increase in torque or horsepower as the specialty cams. But they provide a general increase in performance across the RPM range.
No one cam can do everything, if that were possible. That's the only cam we'd make. If you're looking for huge increases in low end torque and top end power, what you really need is a bigger motor and rest assured we'll have a cam for it. Now that we understand some of the theory behind the big three cam specs, let's take a look at some cam specification charts. In this chart we have the big three specifications for five S&S cam grinds for 2007 to 17 Harley Davidson twin cam 96 and 103 engines.
The first four are Bolt-in cams. Since the lifts are not over 585 these cams will work well with stock cylinder heads. Although porting the heads will certainly improve the performance. The fifth grind is a high lift cam and will require the use of special high lift valve springs. This cam is designed for larger displacement engines and will only deliver its full potential with ported heads.
Now let's take a look at the timing specs. The first cam is the S&S OES original equipment specification cam. This one is basically a stock replacement cam shaft with the same specs as a stock cam. So we can use it as a baseline to compare the other cams too. Let's take a look at the intake opening and closing times.
Performance cams always open the intake valve before top dead center on the exhaust stroke. That's why that column of the chart by default indicates before top dead center numbers. But not this cam. The negative nine in the column indicates that the valve opens nine degrees after top dead center. So the piston has already started moving down the cylinder on the intake stroke.
All the other cams open the intake valve before top dead center. So why do the OES and stock cams open it after top dead center? The reason is emissions compliance. Keeping the intake valve closed until after top dead center. And in fact, until after the exhaust valve is closed is a way of reducing hydrocarbon emissions.
It's nearly impossible for any unburned gasoline to be sucked all the way through the combustion chamber and out the exhaust pipe by the vacuum created by the escaping exhaust gases. Since the exhaust bell is already closed. The OES cam closes the intake valve at 25 degrees after bottom dead center on the compression stroke. So it does take some advantage of the continued air flow into the cylinder after the piston has changed direction. The intake duration of the OES cam is 196 degrees easy to calculate from the numbers.
It opens at nine degrees after top dead center. Bottom dead center is 180 degrees from top dead center. So when the piston reaches top dead center the valve has been open for 171 degrees. The valve closes at 25 degrees after bottom dead center. So we add the 171 and the 25 to come up with 196 degrees of duration.
If the intake valve had opened before top that center we'd have added that number to the 180 degrees instead of subtracting the nine degrees as we did in this case. Let's compare the OES cam with the S&S 551 cam. The 551 has 550 lift which is definitely higher than the 474 lift of the OES cams. That makes sense more air, more power. The intake closing time of the 551 cam is actually six degrees earlier than the OES and hence stock cams.
That may seem a little odd, but remember that the 551 was designed to improve torque. It does that by closing the intake valve earlier more air is captured in the cylinder, combustion chamber pressure is increased. So the engine makes more torque at lower RPM. You may wonder why in spite of an earlier intake closing time the 551 cam has more intake duration than the stock cam. That's because the intake valve opens 26 degrees earlier.
Looking at the MR103 cam specs. We see that the intake closing time is quite a bit later than the OES on stock camps. And it has 30 degrees more intake duration. The MR103 is a mid range cam that's designed to improve performance across the entire RPM range without an emphasis on torque or tap in horsepower. And that's exactly what it does.
Comparing the HP103 cam with the MR103, we see quite an increase in intake closing time and duration. The HP103 is a horsepower cam. It's designed to maximize the top end horsepower of an otherwise stock 103 cubic engine. So the intake closing time is later, but it's not extreme after all the HP103 has to work in the stock displacement engine with stock compression. Comparing to HP103 cams to the 675 cams.
There's a big jump in both intake closing time and duration. The 65 is also a horsepower cam but unlike the HP103, it was designed for large displacement high compression engines. The high lift and the radical timing are going to work well in that application. If you were looking for a cam for your stock engine and you chose the 675 because of the big numbers you would be sadly disappointed in the results. And you would have spent a lot of extra money on parts and labor to install the cam.
This cam requires high lift valve springs, roller rocker arms, adjustable push rods, and you'll need head gaskets. Since you'll have to pull the heads to install the springs. Is it a bad cam? No. In a big inch high compression engine, it'll stretch your arms and make you smile.
The biggest takeaway here is that you'll get the best results if you choose a cam that is appropriate for your engine. And just as importantly your riding style. Watching this video isn't going to make you an automotive engineer but I've shown you the basics of how you can compare different cams by their most important specifications. You should be able to get a pretty good idea of which cam would be the most appropriate for your specific engine. Of course, if you're considering an S&S cam and you have questions, you can always call and ask our tech department for advice.
I'm sure you've noticed that most cam spec tables contain other specifications that we haven't talked about here. I'll be talking about those specs in the next video.
Share tips, start a discussion or ask other students a question. If you have a question for the instructor, please click here.
Already a member? Sign in
No Responses to “Understanding Cam Specs: Part 2”