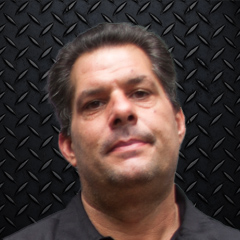
Tips on Extending Your Handlebar Wires
Bob LaRosaDescription
Before we get into actually extending the factory harness, I wanna just take a moment and do a little electrical review. When it comes to snaking this harness through the Mini-Ape, you don't wanna be using any style spade connectors, you don't wanna leave any variables that can vibrate loose or cause trouble in the future. You certainly don't wanna use any style what's known as a toothpaste cap. Even though it will securely attach the wires, if you had eight pair of wire, you're not gonna be able to run it through the bars. These are more well-suited for AC voltage in a home than DC voltage on your motorcycle.
Splice connectors like this, they are very susceptible to vibration and are pretty much wide open to the elements when they're in use. More suited for a trailer than your motorcycle. Again, another style, a twist-on cap. Even if you did it that way, you made your extensions, you'd never be able to feed it through the bars. In order to do this extension, you're gonna have to cut your factory harness, you're gonna have to strip at least half inch, maybe 5/8ths of an inch of wire back not only on the factory harness, but on the same color extension wire.
When it comes to doing that, you need a good-quality sharp stripping tool. What I like to do is clamp down on the wire, make sure you're using the correct gauge allocation in the stripping tool. And then I like to turn and make another cop. This way here, you kinda score the entire circumference of the insulation that you're trying to remove. Then grab it with the extensions and pull it away.
Don't drag it with the cutting allocation. See how that is? You don't wanna cut it and then strip your way entirely off the wire. Problem with that, you run the risk of taking some of the extra conductive copper with the insulation. You don't wanna do that, you wanna make sure all the strands stay intact.
So again, simple as determining the gauge of the wire, making a nice clamp on it, twist it, make a nice clamp, and physically score the insulator covering. Then instead of dragging it off with the stripping part of the tool, use the end and grab it. Pull it away clean, all the copper remains intact. Now, when it comes to joining the two connections, you can solder. There's many, many schools of thought.
Okay, a good mechanical twist, which I'm gonna use a little heavier-gauge wire just for the demonstration. When it comes to a true mechanical twist, you'll strip back just about the same amount of wire. You'll have to use a good-quality heat shrink whether you do a soldered connection or not. You'll find heat shrinks are available in a bunch of diameters and also in an array of qualities. You can buy 'em that they're very cheap, as soon as you heat 'em up, they'll wanna split.
You can also buy very good quality shrink, which is actually adhesive lines. When you warm it up, the glue comes out and creates a nice weather-tight seal. Comes to doing a nice mechanical twist, and again, there's many schools of thought when it comes to joining wires. Some folks will tell you if you solder 'em, the outside of the heat travel path is the weakest point of the wire. So if you solder your copper here where the hottest point inside the insulator, creates a weak spot or a stress riser.
Some people will tell you if you take the wire and bend it, you'll actually fracture the conductive property of the wire because it was heated and soldered. A lot of people will tell you a regular mechanical twist, which I mean, you have to do correctly. You join the two wires, you get 'em to twist together tight so it's the same outside as the insulator, and then you take those two tails that are left and twist those independently from the rest of the mechanical twist. With that twisted together nice and tight, you can see it's fairly weak on its own, but if you take and you twist it back together, this is just a mechanical twist. There's no solder.
There's no heat applied to the wire. You saw it was fairly weak on its own, but if you twist it back together and it's nice and tight, put a good piece of the adhesive line shrink over it and shrink it into place. You wanna make sure you let it cool down. Now, anytime I install shrink, I try to make sure half the length of the splice is left hanging over for the shrink to protect the wire and the splays. But with the shrink in place, you'll find that mechanical splice is fairly strong.
This is a good-quality shrink. If you use cheap shrink, don't be surprised if this just pulls apart. But you'd be hard pressed to pull that mechanical twist apart. When it comes to soldering, again, there's a couple schools of thought. Some people prefer to do a mechanical twist, trim off the excess, do your soldered connection.
Some will prefer to keep the wire in its natural state, once you took the insulator covering off of it and just engage both the ends and lightly press 'em together and then do your soldered connection here. Again, if you have the tools, take the time, use a piece of spare wire like this. Practice removing the insulator, practice soldering. A soldering gun has to be hot. You wanna just touch and dab the solder, the solder should draw into the copper.
You shouldn't have to overheat wire to the point where the insulating covering starts to bubble or get soft. It's too hot. So again, practice on spare wire before you just start to cut into your factory harness.
SOLDER! the twisted splice, where each wire end is wrapped around the opposing wire is called a western union splice (P.S.259 Brooklyn, N.Y. 1956 Jr. H.S. shop class) then soldered and (taped) but modern now, shrink tubing. use thin resin filled solder. Heat the joint then apply the solder, just enough to 'soak' into the splice.
Great video. With emphasis on practicing your soldering methods.