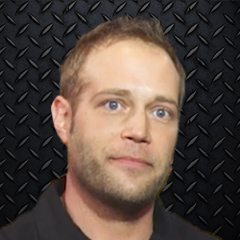
FMH LIVE: Wiring
Tommy CrealDo those wires have your head spinning? Watch Tommy ‘Clutch’ Creal in this FMH LIVE as he goes through a 2000 HD 883XL wire loom. If you’re looking at eliminating, adding or modifying parts on your bike or simply just want to hide the bulky wires, then this is a must watch!
Here’s what Tommy covered:
Re-routing looms
Adding connectors
Specific wires/gauges to use
Various soldering techniques
Play and slack areas
How to properly and safely move looms/components
Wiring and or Electrical might look scary but you can do it. Here are several hours of video on the subject here at Fix My Hog:
Electrical Systems
FMH LIVE: Gauges – Info and Troubleshooting
Electrical Troubleshooting + DVD
All right, let's do this. Hey guys, welcome to this live event with Fix My Hog. I'm Tommy Clutch Creal. This live event is brought to you by Haynes Manuals. Thanks to those guys for hooking us up with all the manuals for these projects.
And make sure you guys get out there and get the most resourceful tool you need in your toolbox or in your workshop. They got everything online as well. A few things before we jump into this bike I wanna go over with you guys, right below the little chat box right there you'll see a link to share your hog with us. Make sure you take some pictures, if you're out on cruises on the West Coast, or somewhere warm unlike us in the Midwest here, drop it on share FMH on #ShareFMH on Instagram and keep us posted on what you're doing, we love to keep in touch with you guys and make sure we're giving you the right content over us here. So share that.
And then also that chat box you guys all see right there, you got questions as we're going down on the bike or random questions about your project that you're working on, make sure you drop it right in there. I'm gonna put some time aside halfway through this project, kind of check that chat box here on my phone and see if I can help you guys out in some of those questions. I'll start with this is actually a 2000 Sportster 883, we bumped it up to a 1,200 when we got it. And we've taken this bike obviously and shredded all the parts off of it and made some adjustment with the flanges in the back here, and this is gonna be turned into a Cafe racer build that we're doing. So over the next couple of months, you're gonna see some video shooting out here and there, make sure you keep in touch and watch those videos 'cause we're going step-by-step on how to take a stock Sportster and bring it down to a Cafe racer build.
A lot of good people have contributed to this build so it's definitely beneficial and some good stuff in there too. My man, Zach behind the camera, he knows all about it. So one thing that we're gonna be going through today in heavy bulk is the electrical system on this. When we bought it used, not, too many miles, I think about 25,000, 30,000, which is kind of approaching a higher end. But the electrical side of this that you can't see when you're buying the bike is what we kinda ran into when we were going through it.
So we're gonna be on this project, put in a new Dakota Digital dash on here, taking the stock one out. New handlebar controls we've got from PM that we're gonna be putting on and also new carburetor and things. We've made some adjustments already to the top motor mount here. So we had the horn right here, that's gonna be relocated to the front, we're gonna actually do that wiring today so we can mount it up there. And then we're gonna be going through and getting rid of all this bulky wiring And as we go through, we're kinda gonna inspect and see what's going on with someone that already had their hands on this project.
So that's kind of the difficult part you can't see like I said, when you're buying bike. You can't visually see the wires under that loom and what they did to hide it. So I'm gonna take you through it and how to properly do it, and in case you do sell your bike and work on it, next how to restore those wires that you may not be using as well. Are we good to go? You ready, man?
All right, so let's rock and roll on this one. I'm gonna start with the components that we did take off on here. So we took off our VOES. And that was mounted right here on the rear on this side actually, but on our top motor mount, right above the manifold. The reason why we don't need this is we're not working with a CB carburetor, we're working with an SNS shorty, so we're not gonna need the vacuum.
It's gonna give us a cleaner look that we're trying to go for on this bike as well. We took off some of this electrical wrap as well just so you guys can see in here, it doesn't take us an hour to do it. But it was pretty bad. And then we were going through and saw a few adjustments that probably the previous owner had and this was actually electrical taped and all it is is exposed wires here. Are you able to see that, bud?
So as you can see, there's exposed wire all the way through and they didn't individually wrap these repair correctly. What you'd wanna do is actually cut this, run new wires after individually soldering those with some heat shrink over it and then put a new insulator on top of it. Glad we caught this now 'cause now we can not obviously fix it, but we did see that kind of stuff. And as we go through here, we're gonna kinda pinpoint and I'll show you some other ways. First things first.
I'm gonna take some of those bolt that we already took off and show you guys over on this side. Not damaging any of this stuff. We wanna make sure we're keeping in real form. So as we took off the triple trees, the risers on this sporty, this was the bulk that we had on the front end. We're not gonna be running front turn signals so in order for us to start cleaning up this entire loom and get rid of all this, my opinion pretty bad chop shop job this guy did, I wanna start removing some of these other parts.
Turn signals are gonna be one thing that we're gonna remove. Obviously, if you have zip ties holding these down, get rid of those, and we did loosen up our ignition coil here. We'll take this off just so we can access this entire loom. So on this side, we have our ignition switch. There's one Allen coming through here.
Pull this guy off. Pull that out, put the bolt right back in so this little guy we don't lose. I did crack these earlier. The ignition coil pulling out. Would you listen to my country music in the back.
So pull the top off, and it's just a backing plate here, so it's not individual nuts going to the mount to the gas tank. So obviously seeing these wires, which you'll see in a little bit, a little bit clear, you can tell that someone did go in and replace the ignition coil on here with another stock Harley. But these are our mounting bolts and bracket for the ignition coil. All I do is move this off and pull these guys. Now don't forget if you're going through your loom and redoing this, don't forget to reroute these through if you're keeping that.
I'm gonna kind of show you the preparation after we get some of this stuff removed on how to route these correctly for you as well. So I'll kind of cleans up some of this for us here. All right, going back, turn signals. This is one of our turn signals right here. Re-route, find the route fort here.
These things are dirty. And we're coming. So right here is our connector for our turn signals, both of them right here. So what I'm gonna do is I'm gonna pull this one off. And on all connectors that we take off, and even if we're not gonna use them again, I like to think of the person that like to be unselfish for a little bit and think of the person that might be working on this next.
So what I'm gonna do is actually label both sides of this connector. Some of them can be the same, but likely not. Turn signal, I'm gonna put that right here. And then I'm gonna put three individual dots. And this is just a marker pen.
So those three individual dots. I'm gonna do the same thing on this side. And we're gonna do that in different variations as well. So that way we know if we ever go back or we sell the bike, we can get these extra components to that person buying it and say, "Hey, if you ever wanna restore it the way you had stock condition, you can plug those right in." You gotta love it. So the way the person that wired this, you can't pull these off 'cause they went right through our loom right here.
So what we're gonna do is we're actually gonna take off ignition coil wires, which are all rusty. And when we redo this, we're gonna have to put new terminals on and put some dielectric grease on here. Ish. Make sure you keep an eye on these small washers as well. Easily get lost.
All right, come on buddy, come on. All right so we're gonna route these back. And there we have one more nut. All right. Screw one on this side, both negatives in the middle is positive.
Pull this off and what we're gonna do is just reroute them and put them right back. I always like just put them right back, so not forgetting what we have here. I know this is everyone's fun area that they can't wait to start working on their bike, but nowadays with all these street glides and rural glides, these things are pretty prominent on electrical. Actually, we can get a jump this over one. Pink's going on another negative.
This is a single fire ignition. All right. They had originally spliced this, which we won't need again. So we're gonna reduce that when we get there. It's a job for smaller hands.
All right. All right, so we've got those back on, make sure we just don't lose them. Let's get these turn signals out of here, here's one of them. And then two of them. Obviously here's our three dots on there, representing which one goes right back into it again.
Get these guys over here. Secondly, so we're gonna be, obviously I said earlier we're gonna be putting on new hand controls and levers and all that stuff from PM. This one, we've wrapped up the stock controls and configurations here. We're gonna unplug these and push them to the side. We're not gonna use these connectors, we have new connectors that once we route the wires through the handlebars, drop them down for that clean look, then we'll come through and actually put the connectors onto those.
What we're gonna do is same thing with these, I'm gonna mark these. I'm gonna put one on here and then two on this one and then same thing on this side. And keep in mind, the biggest task with electrical and once you get into redoing this or hooking up new components is making sure you're keeping track of the right wires. What I mean by that is, make sure you're going through your manual, and we're gonna dive into the manual in a little bit, looking at the wiring schematics, but a lot of these wires can be cross-referenced, meaning if someone has already gotten their hands in here and not fully respecting what the manual has to offer, and not color-coding everything correctly with proper tracers on those wires as well, then you're gonna run into issues with crossing wires over and potentially ground turns into a power somewhere. And that's a big issue.
Make sure you just keep track of your wires as well. On the top of the manual here, I have masking tape I already ripped out and made some labels on it. The reason being is that some wires that we're gonna be cutting later on this event, we're actually just gonna wrap them around there and then we're gonna hide it under the loom. That way in the future, if anyone ever wants to pull it out, or if you're gonna do some other changes in the future, you know exactly where they went. Obviously we're all human, we forget stuff so make it easier on you.
Taking pictures throughout this entire process, we do that with a lot of our builds and restorations. We take tons and tons of pictures. All right. And these are obviously seal connectors, waterproof. Same thing with the plugs that they use on here.
So we have one of our controls right here. Like I said, we're gonna be using the exact same plug when we put in the new ones as well. Nothing's clean on this bike, holy cow. And then our second one. As you can see, that kind of cleared up quite a bit for us, just at least on the wiring up here, a lot less connectors.
This goes in between our risers up here. This clamp will be put back in place. So it hides it up there, it's a two-clamped piece between the rises so you don't see it at all. I think we have a majority of what we need off of here. We've got our horn that was originally on here, they tap, they did a ground right here to the top motor mount.
We're gonna be pulling that forward. Next process that we're gonna go through after obviously getting everything off that we're not gonna need is gonna be starting to consolidate some of the wires. Later on, we're gonna be putting on the dash. What I wanna start to do to make sure we have a nice, smooth loom that doesn't have any cause of getting binding somewhere or get into running part or moving part on it, is to keep it nice and slick going through. I don't want these bulky wires to be popping out here.
We have a gas tank going on that rides right on the backbone with a little bit of dropdown on it. I'm gonna try doing our best to get this thing snugged up right here and routing through. Before that we're actually gonna do is gonna pull off these connectors right here. So the turn signal for the fronts, we're actually gonna take these wires. I'm gonna pull the loom down here just a little bit.
And all I'm doing is taking a razor blade. Pushing away from you, don't pull back on these, and keep your fingers out. I've seen guys try to do this. And while so when you're putting your razor blade or tool in here, make sure not to jab right through the loom. What is gonna typically happen nine times out of 10 is that you're gonna hit a wire and open that insulation, so then it's exposed.
So try your best to just get the loom like that and not go directly in on it right there. We're actually gonna take scissors. And you can see I'm trying to push away the wires. That way I just get the tip here. And we open up just a little bit.
And then we're gonna take this around, away from all the wires. And I'm not too worried about keeping the cuts exactly straight 'cause we're gonna be running some heat shrink and some flex around these wires as well. My man Zack over here knows how detailed I get on these wires to make them look nice. So that's him huffing and puffing. And it goes to say, you guys all know craftsmanship and the pride in the work you do, so take your time while going through this, make a big dent.
And always is never fun clipping a wire that you don't need to clip. All right. So we do have that disconnected. Obviously we're clipping wires and disconnecting things. Our battery is removed, that would be the first thing you do before any electricals.
Unhooking your battery and your module just to prevent any kind of circuit or voltage going through that you don't want and kind of ruining one of your modules or something or your ignition. I'm gonna do a clip right here. The reason being, you don't wanna go directly up to the connector right here. You're not gonna have any wire to get exposed if you wanna put this back on later. So if we come down about an inch right here, that's enough wire to redo.
And then also we're gonna put some heat shrink over each one of these and then one final loom as well. Now, if you weren't worried too much about the bulkiness of this loom, you can always keep this, wrap it up in here, and then put it up. Personally, we're just gonna keep this nice and sleek and as tight as possible so that's the reason why we're also cutting it. All right. Ready, Zack?
So our here's turn signal module. I'm actually just gonna plug it right into the module, the connector here itself so we don't lose it. I got a ton of heat shrink here. So heat shrink all it is, it's a preventative from allowing exposed wires to come into contact with each other. So what we're gonna do is we're gonna take about half an inch on each one and we'll use scissors on here.
I'm not sure . Right here? I'll bring it up. So how many wires we got? We have six wires.
I think our turn signals are moving behind me. And we have different sizes of this heat shrink as well, and I'll show you that now. So we use this on every wiring job that we do just to help prevent anything in the future from happening and also helps keep those wires secured. And then this glossy flex you see in the middle is just more of an aesthetic that we put on over the heat shrink, which also we have different sizes of as well. You'll see how tense we get this one.
So what we're gonna do is we're gonna put these on, we're gonna leave a little bit left on the top. That way we can heat shrink it and not have the wire pulling. Take a steady hand for this one. Glad I didn't back off from the coffee today. All right.
And then we're gonna just take our heat gun. And notice when I do this, I'm not right up against it, you're gonna burn right through it. You can take a lighter butane torch, do that as well. Make sure you're in distance of it and gradually go back and forth through the heat shrink to get it all mesh and even with one another. All right.
So there's two different diameters. We know we did a right job on that just by having the tips here. There's no wires in there. And now just because I'm me, we're gonna take one more piece of heat shrink, put it right over the top of that. Actually loving this wire.
Zach absolutely hates when I cut wires and start wiring stuff. It's a panic attack waiting to happen. I'm gonna tuck it down on the loom just a little bit so it gets snug in there. Is it not? Oh, I thought I did.
Some of the bigger heat shrink area you're gonna actually need to work around it. But simple as that. So that connector then turns into all our wires right there, they're all secured right where we need them to be. Now we're gonna do the same process right here to our four pin. Now remember I said, taking labels and notes here, so I actually did make a note for this one.
So front turn signals. What we're gonna do is gonna wrap this masking tape around it. That way we've got it ready for the future. And we're gonna have this all covered as well so you won't obviously see that in that masking tape. Tuck that down.
We'll do the same thing here with our front. Clip about an inch away. Then go through and also do. So used to having these heat shrinks right next to me. Do the same thing.
So we need four for this one. And as you're going through, see this, take a look. Obviously they split off on here. We can obviously go up here and do that, I'm not too worried. We ain't gonna run into any issue, it's not a hot wire.
Come on, there you go. And what I got, I did notice this, this is actually a four pin, if we were using a tack on here. So that's why we don't need this one either. All right. Double check, make sure they're not pulling.
And then rather than doing one on here, we're just gonna do this sort of piece of heat shrink on that one. I'm gonna use a smaller diameter. Soak that over. And also it gives it a nice look too. If you're not looking to make it especially sexy or aesthetically pleasing, you can always use heat shrink as you route through.
For your loom. And then also if you're heating with the heat gun or solder, or anything and your gas tank is still on there, or you have some kind of flammable you just cleaned up with, carb spray somewhere near your carburetor, honestly, make sure you're not using your soldering gun right around there or blasting that heat gun on there. You're gonna have a bigger issue than you ever anticipated. Work safe on your bike as well. I know we wanna get it done and get it back on the road but take your time with it as well.
So I'm gonna take some electrical tape, I wanna make sure these wires are kind of secured away. We're gonna wrap it around. Get that loom nice. Get it to start to come together. All I'm gonna do is just one little strap.
Making sure we have no wires binding. That's already less bulky back here as well. I'm gonna do one more up there in the front. Right under here. You'll see some jobs where guys take the electrical tape, wrap the entire loom with it, all the way through, you can do that.
Over the years what happens is that the electrical tape actually gets wet or starts getting dried out a little bit and it just starts flaking off. That's the reason why we typically don't use electrical tape on all our looms, we use the insulation that doesn't wear down, I don't specifically know a lifespan of it, but it is a lot longer than electrical tape for sure. All right, we're gonna pull the horn wares through since we got those off. And this is our ground wire for it. We can either find another ground to route through or use this existing one, so we're gonna actually just use the existing one on here.
And then I'm just gonna bring that through and down here so it's in place for us. And as you're going through and working on your bike, one big point I can make in all the wiring is to make sure that you're routing in a safe position. If your triple trees don't have an internal or external stop and they're slopping all around the place, make sure you're not routing right down the down tube or right in between one of the points where the top or bottom tree is gonna hit right there, obviously you're gonna pinch. Likely ground out something or start wearing down in that wire as well. And same thing on your mounting points with gas tank.
If you're mountain a gas tank similar to this one and you're trying to go on the backbone, which we wanted to do, but we don't have enough space, once you clamp down on that back here, it's gonna pinch down that entire loom and then start getting some interference with the wires. Think about it, kind of think it through before obviously cutting wires and putting new ones on that route and so. Now that we've got those clipped off, what I'm gonna do is actually zip tie this into place where we want it so we can get the correct length on these wires. So I'm gonna start back here. And I'm only gonna use two because we do need to route one of our wires for the speed sensor, which is gonna come back.
I just wanna get a general reference. and we're gonna obviously be clipping this one and putting insulation on that as well. All right. Man, this guy made a mess. Let me see if there's any questions or anything.
Make sure you guys if you have questions, drop them in that chat box. All right. Did you say why you cut the front turn signal wires? Why? Yeah, why you cut them.
Just to reiterate, so cutting the front turn signal wires, that connector right here, we're not using the fronts on here, we're just going with rear signals. Legal in where we're bringing the bike, so we did check on that. But also in the future, you wouldn't probably wanna do that. I wanted to do it just to have a nice smooth loom going through here. It'd be two connectors right here that would be bulking out.
So just to keep it kind of consistent all the way through, it's gonna look like this rather than have bulky all over the place. All right. I'd like to jump onto actually the ignition. So first things first, we're gonna look and see on how he initially routed, where it came through on here. There's a lot of excess wiring here, so we're gonna take some zip ties, find our own wire configuration here.
I wanna make sure we don't have any other wires in our way. So I'm gonna go through right here. We do have a front clamp for our rectifier. So I wanna make sure that we're gonna not interfere with that, but hide this wire as best as we can. Obviously you can clip these too.
I just like to keep them on there until we're all done with it. I don't miss any of them as well. And you don't wanna do these too tight either. I've seen it where you crank down on it so hard or using stainless steel zip ties that they have, that you typically use on exhaust pipes. But you can actually pinch down the wires on here too.
So make sure not to crank entirely down on it. You still have movement with the wires in there as well. All right. So now you can see here's our ignition coil, we're gonna pop these out. Just for my reference, things were running good before so we're gonna put reference points on here too.
I'm putting it on the inside here so we'd actually don't see it. We'll put it back on. Marking, pictures, all that stuff, I can't reiterate enough, no matter what kind of project you're doing or how in-depth it is. Make sure that you're just keeping track of these wires. All right, so let's pull these off the ignition.
We're gonna make these shorter and put a loom over it so we don't see all that stuff right there. Got the spaces on this side. And what I'm gonna do, see in our manual. Already marked the pages as well. Everything is color-coded for us right here.
And I already made notes for our dash up here which is gonna go to which plug and play on our speed sensor. And if you've never gone through wiring schematics before, here's a quick tip. Everything's color coded. Tom Tony is here. Varying on the stock if it was stock set up.
But you also have your traces. So those little dashes you see right there are tracers on the wire like this. You see an orange with a white tracer. That's what you wanna look for on here. And then also when they intersect, or you see a dot right there, then they're actually connecting to one another and following the entire circuit.
So when you see a jump through or a right angle, they actually don't intersect, they're just bypassing. So it'll make this a little bit easier on you eyes. And these are all connectors that you see as well. I went through this, someone did play around with how this is all set up. Obviously this was running when we bought it, ripped around on it for a while.
So what I'm gonna do is actually hand write down which side we have. So we have two minuses, this is a single fire, two negatives, and then a positive. So blue is gonna be on the left side. We got white in the middle and then pink on right side. Let's pull these off.
There we go with our ignition coil. You can see the dots I put right inside here, that was not noticeable you won't see them as well. And your zoom game is on point. As you could see all of the slack right here. And this guy's makeshift connector with this looks not the best by any means.
We're gonna unplug this one and redo that as well. We're gonna hold this up, route it, and we're gonna cut these way back. And this is for a tack, that's why he had this stuffed in there. I'm gonna bring that back and that way also if we need to route this around a little bit differently. And what I'm gonna do is I'm gonna take.
So we're gonna cut. Let's double check on this. We're gonna cut, bring them in. This is gonna be our point where we wanna route them so we're gonna have to be back here. I'm just gonna make a mark and then I'm gonna get rid of these.
And this is the tricky part where you don't wanna take side cutters, your wire cutters and go right through the sleeve. I like to push all the wires down, get a loose end right here, and then I poke right through, and make a mark that way. So we at least open it up and we'll do the same again. Avoid cutting any wires that we don't really need to be cut in here. And you can see I'm not pulling on this loom either, while I'm doing this and going like that, reason being is that you can pull those connectors out.
I'm holding the wires like that to prevent any unnecessary damage to this. You can see even that small stuff that'll cause issues. We've seen it, we've been through it for many, many years. And then there's a sleeve that we don't need. We're just gonna double check.
Route that up and we'll be good to go. All right, so like I said, we marked blue, pink, and white. Those are gonna be the ones we wanna keep. I'm gonna wrap these together. And then we're gonna cap off the other two.
One usually goes to the VOES and the other one goes to your tachometer as well. So we're gonna take these, we're gonna do the same thing. I'm gonna cut them down just a little bit more, put heat shrink on them and tuck them right back in that sleeve. Usually we run into a ton more on these electrical projects than we are right now. we need to do more of these events for you guys.
Pull that down. Put these up in here so we're not getting them off. Obviously you have a buddy or something to help with the Saturday, it's always easier with putting heat shrink and soldering iron when you have someone around. To hold things in place as well, rather than being a one-man band here. All right, so these are on.
Were gonna tuck them right back in. I'm gonna do it at different ends on this. And then run a piece of electrical tape just to make sure those don't pull out. So you can see that you don't need to go through this entire process, just something that became habit for us. It's very detailed, but make your life a little easier.
All right. So that looks pretty good. We're good on slack, obviously we don't have anything behind your moving parts around it so we don't have to worry about having additional slack to it. We'll put the connectors on, but before we do so, I wanna make sure it looks good as well since that's a visible loom coming through here. So we're gonna take some of our black sheathing.
And a quick tip on this, if you are using this, it loves to fray out. At the back end here it is expandable, so you can't get your finger in there as well for bigger looms and different sizes. So what I like to do is I like to take a piece of electrical tape, wrap it around very loosely, that way you're not constricting it and it can still expand just a little bit. And then we're gonna cut right in the middle of that. Sharpest point you got.
And that way it doesn't fray out. And we'll do it to the other side, but I wanna see first how much we have to kinda go through here. And then we're gonna take another easy little tip to. When you are routing your wires or your loom through and you don't have a sheathing like this, turn these like that. Reason being is if you have them forward, they're gonna poke around and bend around in that loom and it's gonna make it a lot harder for you.
So push them over so you have no spot work and get hung up as well. So we're gonna start on this end. Just make our way down. And I guess we could go all the way down with it. And I might as well, right, Zack?
Of course, why wouldn't you? It's that little extra touch. So we'll take these off. We obviously got our measurement from that so push this around. I'm gonna go all the way down with it.
Almost right down to where it tucks in on the bottom frame rails. Perfect. And then we're gonna feel for where these wires are. So they are right here. I'm gonna take some tape.
Right in front of the wires, do the same thing. Cut those off, obviously double checking to make sure you're not cutting on those wires. And then what we're gonna do is pull back like that. See when I do this, actually you can see the difference in the width here and the width here. Reason being, as I pushed this far, far back, that way we can get this done and then pull our sheathing up to cover the entire wires.
All right, next up what we're gonna do, put some heat shrink over these two so we can saddle them up to new connectors. Some zip ties along around here. We'll strip the insulation. I'm gonna wrap these around. And then we're gonna get just a size larger heat shrink for these.
Reason being is then we can actually put them over the connector, make it even look that much better. I'm gonna bring these all the way down. That way, we don't heat them while we're actually soldering. Putting that. All right, so two ways of doing this, you can actually just crimp on your connectors as well.
I personally like to crimp and solder at the same time. Definitely for battery cables, if you're making your own battery cables, drill a hole through that terminal and actually crimp it and then fill that whole thing with solder, those have the tendency moving back. Same thing with starter wires. Even if you're using a high-end riveter, and it'll make your job so much easier Less complicated in the future. Let's get some connectors.
We have our eyelets right here, connectors. What I'm gonna do is actually pull off. I'm gonna get some needle nose on here, pull off the insulation. Just holding it right there on the top end. And then I'm gonna pull off the outside.
You sure? Yeah Right here I'm gonna hold this end. And then just pull off the insulation. I'm gonna do one more here. Get that out of there.
All right, so let's crimp these on. We don't want too much wire up on here, so let me draw that back. This is why I don't do it. No matter how hard you crimp sometimes they always like to walk off on you. We have a little too much wire on this one for these terminals so I'm gonna cut it down.
You don't want it interfering with that eyelet. It won't mount correctly and then also you want your second crimp on this to hit the insulation. So one on the wire, one on the insulation. I felt the ton better. Draw back this wire as well.
And then I'm gonna get a new terminal. This one right here. All right, looking nice. Out with that, man Make sure you're closing those boxes too. How many times have we flipped over those eyelet boxes?
Many times. Right? It's a great job for your kids if you wanna try and keep them busy and you accidentally hit those or cotter pins boxes over, sorting them back into place. Limit the swearing though. All alright, let's get this one popped down.
Steady hands for this one. So I'm actually pretty happy with these crimps. We're just gonna crimp these on and put a heat shrink over, I wanna get with the dash with you guys here today too. All right. We'll take the heat shrink or run it directly up like that.
You see that, buddy? Yap. Getting stuck on me. Come on now. All right.
So got them like that, and then we'll just heat it up. Always happens. Just dropped down on me so I'm gonna redo this and turn them sideways. Obviously make sure your fingers are out of the way of this heat too. All right, so we have all three terminals put back on here.
What we're gonna do is we're gonna take our sheathing, pull it back up, I'm gonna get it over this little hump right here. Come on, come on. There you go. You let that slack up. And once we get them in place, we'll be able to expand this all the way up.
What I'm gonna do is, we're gonna take this back now. Zip tie it so we get the sheathing up. You can see on the down tubes already looks better. Make sure not to do these too, too tight. Now it's a lot less wire just right there with that.
We running that right in. All right. Secondly we had, these are our wires for our ignition coil, one was the ground one was the wire. Now, considering what they did before is they just put a connector right here on our signal, and then the other one actually goes to our kill switch. What I'm gonna do is just remove this connector altogether.
I'm gonna take our ground here, I'm gonna cut it, go through and just make our signal go through. I don't know what they did on the backend all the way through here, but we had no issues whatsoever. Tested it out with our multi-meter to make sure that there wasn't any issues with resistance in ohms. So what we're gonna do is just clip this real quick, and that'll get us all wrapped up with our ignition set up. So we've already labeled a few so we're gonna go forward on these.
The only reason why I'm still doing this even though we're taking it off together is if it ever comes disconnected and we still have it. See I pulled that off. As you can see how long this one is, we're just gonna take another inch off. That way it drops with the other loom right here. We can keep those in sync with one another.
And we're just gonna actually take our heat shrink off that altogether. Then another inch off this one. It's almost like painting. Take your time. Things at the end come out and look good on this thing.
And it also helps when you guys are doing your project, to order some extra heat shrink and some of the flex wrap, it'll help in the long run. Hate these things. Give me a hard times here. Heat this one out. Then we'll eventually tuck that one back here.
We're gonna put some heat shrink all the way through that one since we will be seeing that wire. I'll take another inch off. Bring that up. We'll be pulling that electrical tape off, so I'm not too worried about the length of it right now 'cause we'll get to it. Take some of the top off.
One more connector terminal for this. We'll get that one right on top. Keep in mind, you do wanna check the sizes of these terminals. Those eyelets do vary independent on the stud that you are trying to put that on. That'll be a big difference.
Voltage regulators go back to the battery with their one constant power so make sure you're using a larger one for that for sure. All right, so that'll be the... Holy cow, are we flying through? So that'll be for our ignition coil right here. So these four are gonna go directly up there.
Before we hook this one up, we're gonna put sheathing all the way through this entire loom back here. And obviously we're not gonna be able to cut everything in the front, and slip over our flux wrap like we are with that. But what they do make is a split wrap this, we have a different diameter size for it. All it does is split off and you can wrap it directly around your loom, smaller loom for this one, and then I'll have that consistent nice look. So if you're in a predicament where you can't rip off the connector and you can't fit over the one piece, just use a split and then you'll still be able to kind of accomplish that nice look to your loom as well.
All right, so we're happy with where we're at right now on this. I know we're kind of running out of time a little bit here. I didn't expect to take that long but I do wanna show you one quick thing on our Dakota Digital. I guess we won't get to the horn then today. Bummer.
So this is the new Dakota that we'll be hooking up on here. Three and three A's face. It's got a bunch of cool stuff with the directions of the kazoo for you. So it's hard to kind of go wrong but they prepackage everything well with the wires. And we have four different sets of wires.
One of them is optional depending on if we have a tack or not, which will be our four pin right here, so we won't be using this one. This is our speed harness that we're gonna hook up real quick right now. And then these two go off to the ignition, and then this is also our indicator lights. We'll be using these three, won't be used the tack one. So the good part about these are super interchangeable.
All we're gonna do is we're gonna take our fingers, don't put it right here at the connector, and pull the wires out, come here, straighten it out. All the way down as best as you can, these things are right out of the factory so they can be a little bit stiff. You can see how long the speed sensor actually is. A guy that long for whatever reason. So what we're gonna do is just disconnect this one.
Pull it off, I'm not too worried about clamping it. We'll eventually be cutting these wires right here to hook up our new ones. I'm gonna put that over there for now. We're gonna plug in our new one right here so you can use some dielectric grease as well in here. But this is a waterproof tight connector so you don't need to.
Make sure it clips, seated well, pull against connectors, not the wires on the outside. And then we're gonna figure out or configure a way to run this. I'm gonna put a zip tie right in the back. As you guys can see, it does take quite some time to get the wiring down right but at the end of the day, it's worth it. And look what we got done in an hour here but it's gonna look pretty darn nice at the end of the day.
Okay. All right, so we're not gonna go through and zip tie these all again, I'm just gonna route them up. I'm gonna stick it behind here so it sticks. So we're gonna have access to this, which is okay, because in our rises up here we have that built-in clamp where it's a two-piece, where our connectors are at for the majority of our front end items. So what we'll do is we'll actually just run this up, bring it up here right in front of the gas tank, then we'll wrap this around and zip tie it, and then making sure we have enough length for our steering radius on the bike as well.
That's all simple pretty much our speed harnesses on here. We're gonna wrap it up, keep it up there. Now we're gonna get into the fun stuff real quick. This is indicator lights, that's our panel right here. This was our old backing plate for our speedo, the stock Harley.
This is our pin for it, and then here's our trip reset for it. So we're not gonna need any of this stuff right here, it's just gonna be built in for us. So I'm gonna take this right off. And if you do actually wanna use these on another thing, you're gonna have to clip the wires of this item, there's no way obviously you're pulling through on those connectors. Look how clean it is already, my goodness.
My goodness. I do wanna mention this to you guys before, in this show is that... We have too much stuff around. I'm still trying to make sure you guys can see it though. With any new electrical component, no matter if it's crane cams, if that's Dakota Digital, PM, you're gonna get wiring instructions for it and going through it is gonna be your biggest thing.
What I did is I actually went through here already and it shows all four individual connecting points and just made notes on it. So security system indicator right here is an option with this one, cruise control, engine indicator, and output speed signal. So for three of those with the cruise indicator, and engine indicator, I put no for there. So I know for sure we're not gonna be using those. Speedometer, obviously yes, tachometer, no, we're not gonna be using on this one.
So we can get rid of already one of these connectors right here, which is gonna be the one I showed you earlier. And then our optional four pin for the tachometer. So that was the one we did take off here. So if we chose to put a two gauge on or even a different setup that we have existing with this Dakota, we'd bring these wires back, put a connector on and then we'd just be able to do plug and play with it. But for this, I went through and made the notes.
So white, red, white with a red tracer, red, black and yellow. Yellow is gonna be our signal. I know some of you might just say, you just said output speed signal, obviously you do need that. Yes, it's right over here so it's on our other set right there. And as I went through and did that, I did the same thing in our wiring schematic here.
So I went through and indicated the wires that we are gonna need. So I put orange and black is gonna be our 12 volt fuse, red is gonna be our key on 12 volt constant, black is gonna be our ground, and then white is gonna be our signal. So then we know white's gonna be going to yellow, red is gonna be going to red, orange white is gonna be going to white red, and then black to black. That's the best variation that we have, and easiest way to kind of keep track of this as well. So go through this, study it, if you're kicking back one night, I don't know, sounds weird, but I like to look at this stuff at night and read up on Harleys in their manual.
A great little reference tool for you as well. We're not gonna be able to get into that, it's gonna take another 15, 20 minutes to get all that stuff wired up and hooked up. But a couple of things I do wanna mention before we kinda wrap up the live event is that, as you're going through your wiring, one of the biggest, biggest things is making sure you have enough play on these wires in these looms. I can't express enough how many bikes we've seen come in, it looks like a chop shop, or even masking tapes used instead of electrical tape, not the right connectors, not only will your electrical components not work as right, or as good as they should, but it looks like trash. And then you just take pride in what you're doing.
But as you're expanding those wires with electrical tape or heat shrink, makes sure that excess wire is there for turning radiuses. Definitely if you're working from the end forward and you have a swing arm in there and you're not running a rigid, which most bikes are nowadays, take into play or take into consideration the play of those shocks and how much that swing arm is gonna move. Obviously you don't want things pulling in the back, brake sensors, same thing in the back. Some of the older choppers we work on, they've got brake sensors built in back there so you've got to take that in consideration. So make sure you have enough access, make sure you're taking your time, making sure the crimps are good, the soldering points are good, and then you're also wrapping it correctly.
Like I showed you earlier with the speed sensor where it was frayed out, those wires all it takes is to rub against each other, and it's gonna blow your entire ignition circuit. It could potentially blow out your ignition module as well. Those little things are what to to keep track of and watch. Also just making sure you're not binding your own wires here and making sure you're doing it correctly and just taking your time. I get it, wiring is not everyone's favorite thing to do, it's not my favorite thing to do, but I like to see the end product and how well it looks and take pride in that.
Just take your time and have fun with it. Thanks again to Haynes for teaming up with us on these live events. Make sure you grab one of their manuals, you've got everything and anything out there you can think of. And before you guys go, hit that link down there, go on Instagram, like Fix My Hog and #ShareFMH for us. And so we can see your hog, put it out there, blast it out there, it gets you some exposure and credibility too.
And thanks for joining me, will see you next month.
Share tips, start a discussion or ask other students a question. If you have a question for an expert, please click here.
Already a member? Sign in
No Responses to “FMH LIVE: Wiring”