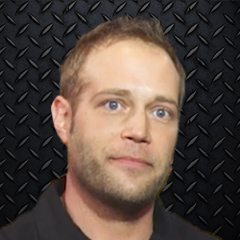
FMH LIVE: How To Fabricate a Gas Tank Part 1
Tommy CrealHave you ever wondered how one-off gas tanks are made? Or better yet, have you wanted to build your own and don’t know where to start? We’ve got your back– join us FMH LIVE with Tommy ‘Clutch’ Creal, where he hosts Part 1 of fabricating a motorcycle gas tank.
Tommy cuts, bends, forms, and welds an entire gas tank by hand while tossing out the do’s and don’ts. There are many factors to take into consideration while constructing a gas tank, such as the type of metal to use, gas capacity, type of welding, fuel injected or carbureted, clearances, bung location, gas tank cap and as you might have guessed a lot more. So, if you’re interested in building your own gas tank or just want to watch the process, then join us and watch Tommy’s craftsmanship come alive. Be sure to check out Tommy’s Part 2 video, too!
Hey guys, welcome to this month's Fix My Hog event. I'm Tommy "Clutch" Creal with High Compression Garage and Chopper College. Today we're gonna be walking through how to build a gas tank. And I'll go through the steps, the tools, things you can use in your garage to bang one together and also some areas to take into consideration if you're doin' it. I've had years of doin' this stuff.
I get that it's intimidating. But there's things we should know why, so I'll walk you through the process today and have some fun while we're doin' it. Before we get into things, I wanna mention to you guys to check out the Rig Your Ride Sweepstakes we've got going on right now. Go ahead and there should be a button to click right there below you. Click on that, sending off August 9th.
So make sure to get in there before then, and giving away some pretty cool parts and it's helping, so make sure to check that out. For some of you that didn't see me last time, I've been building bikes for 10, 15 years now. All the way from corporations to also some celebrities as well. So this is nothing new to me, and it's kind of second nature. All right, let's dive into the fun stuff and get going.
I'm gonna walk you through the tools and equipment. Some of you that tuned in last month, I believe I covered the tools and their purpose. I'm gonna go a little bit more in depth today. And also, just gonna show you the major purpose of these tools and also what we should consider, so. When we're doing gas tanks, for instance, we have a sort of a tank right here.
It's got rear mounting and front mounting. And then below, it's got the EFI right in there and the vent. So when we do gas tanks, it's not that hard. I'll tell you that right off the bat. It just takes some patience.
Outlining and mapping out what you're gonna do, and then also figure out how many pieces you're gonna do and stay with that. So for instance, if we were to replicate this tank right here and do this, we would want to first do the same diamond pattern design. Make that first, and both sides and the top. And figure out if we're gonna do it two piece, one piece, or even a three piece tank. And what I mean by that is that when you're building tanks, you're either gonna have one piece on the side, you're gonna have a top piece, and you're gonna have a one side piece.
I normally do two piece tanks. So it's gonna have a top piece and then we're gonna wrap it all the way around. So today we're actually gonna start with the top piece and then do the sides, get that smoothed out and work around. So next month we can clean it up and mount it. So, let's see, that's the plan today.
And let's see if you guys can do it. So a few of the tools that I went through last time with you, we have a shot bag. This is actually filled with sand. You can use BBs in here. This is something that's relatively cheap.
You can get and put it in your garage. But critical piece to doing metalworking and metal forming. And metal forming is just allowing the metal to work itself, and all you're doing is working around ground tools. So these are dollies, these help us get the corners, the radius that we need. You can see this shoehorn is a little bit more, it has a bigger contour in the front, longer on the back end.
And then our other tool. These are primarily the ones I use. I have maybe 70 different kinds of those. Then we have bossing mallets, or rubber mallets. Teardrop mallets, whoever you're talking to, there's plenty of names for these.
These are critical as well in metal forming because with our shot bag, what we're doing is putting the metal on the surface right here and pounding away on the metal. And this is actually, this radius right here is stretching the metal apart and allowing us to get the contour that we want. It's gonna look like a bunch of shotgun holes right there and all over the place, but that's the start that we want when we start looking at gas tanks or even, for instance, if you're going fenders, even. Or headlights and their housings. You're gonna start working the contour around them.
So these obviously come in different sizes. And we'll go through that a little bit later, but we're gonna be using all three of these at some point to go around and get bigger indentations where we need them, and then smaller ones around mostly the corners that we use. All right, the other is my handy-dandy mallet that I also use. This back end, put my back finger on here, and use this also. I use these with the dollies, so these mallets and hammers are critical as well.
Good old files, hand shears. If you're working and you have too much metal, you can clip the hand shear, cut off even, and get that off even with sanding paper or a power sander to get that as well. Now this little chisel, this is for what we're doing a couple tap welds. And I'll get into this more in-depth later, towards the end of this segment. But if we're doing a two-piece tank, for instance, and we're putting together two halves, what we wanna do is actually lift up on one edge and make sure that's a flush mount.
Typically you're gonna have an indentation, somewhat in a sloped v at the top or on the sides. And this helps give us a better angle to make that flush. And then we would go through on the pressure hammer and English wheel to smooth that all out. So I use these, you can use a flathead even. But I always recommend people to stay away from anything that will gouge or put some indents in the material that you don't neccesarily want.
But at the end of the day, that's more work for you. And less, a little bit more preparation is all you need. And you also have here your typical tape measure, all that kind of stuff we'll go through. But most of the major pieces, I'll be working on the English wheel today, this yellow, this is the drill bit right here. The top is the major handle, the bottom's a little smaller with different pounds on the dies and what that helps us do is get different contours on the tank as well and helps us mold it and seals it out at the end of the day when we want that finished gas tank and we've gotta go do paint, top coat, or even film it at that point.
So one of the big things I wanna mention before I continue on to say, if you don't have these tools or even one of one of these speed rollers, those who can't see it on the screen right now, there's a sheet metal plate. You can always make jigs at home and use your creativity that way to help in forming the metal. I've used pieces of wood, even. When I was first starting and sanded down the wood, used that as a dolly, and then worked my way around there. So don't think you need all these pieces of equipment or tools to get you a handmade tank or whatever project you may be working on in your garage.
But it does help with getting it done timely and efficiently. So, the other thing I wanna mention too is metal selection when you're doing gas tanks. I know there's been people recently that have come by my shop and asked me about metals and what to use. And you can obviously go to an aluminum metal, but those are more, I like to say they're, it's like butter soft. It's super, it's very easy metal to work with.
However, at the same time, it's hard to, it can be hard to weld to certain people and also you're gonna mostly use oxyacetylene when you're filming those tanks. You get a nice silk on the outside of that inner weld and you're making that, it's gonna look like more nimble than bulky. Now metal, 16 gauge which we'll be using today, or sorry 18 gauge, is a little bit more versatile metal meaning that it's easier to weld, it's easier to work on, and the material is just mostly just a little bit better. So if you're new to metallurgy, and we'll all possibly have problems with all that stuff. It's interesting, but we'll be walking through that today and anyone first trying to get out there and take their first stab at a gas tank and weld that as well, I'd highly recommend doing a 16 or an 18 gauge metal.
You don't wanna get too thick of a metal, harder to work with, harder to go through. But it is a good metal. So just keep that in mind when you're going through the planning stages of your tank. And so, here's what we have for a couple key points before we dive into working on this tank. When you're working on, with metal in particular, for anything you may be doing, I always recommend having a clean surface.
So I'll grab WD-40, you'll see me using WD-40. That's just to keep the material nice and clean. Get all the debris off, you start getting debris built up and definitely taking it through the jigsaw drill, you run the chance of that debris getting caught and then scratching your surface all the way through. So if you were to take it to foam or definitely powder foam, you're gonna see those marks and gouges after those as well. So it's just taking a little bit of adhesion separation into building this out and keeping your work surface clean.
Additionally, I've gone through and built tanks for years now and if you don't like your final result, you can always start over and try again. Because I've got tanks sitting over here we've done and you've gotta make sure you're happy with the end product. So if you're not okay with it, if it doesn't fit to how you want it to, you're gonna, don't hesitate on tossing that out and retrying it or trying to fix that. So, the biggest point I can make with you is when building your own tank, preparation and building it out. You're gonna see that, we're gonna go through and actually map out some contours and outline what we wanna build.
But that whole stage will give you the guidance for building out your tank. And within that designing phase, you wanna keep in mind that you want to be able to have enough clearance for your arms to actually clear through. You wanna make sure your clipper trees are not gonna bang on your tank. You wanna make sure you have enough clearance on the bottom of your tank to clear your engine, for your rocker box heads and also crossovers. So, there's a few things that we have to take in mind when designing it.
But all in all, take your time, map it out. Put it on collage board even, and use that as your template. You can also build a buck. At last month's event, I went through and naturally I put the buck I'd built. And that one, all we typically did is we cut through the side panels and top piece and held it right up to the buck as a reference point and we knew when we were there on the tank.
So that's always good to do as well. And then, lastly, in preparation and designing these, map out what you wanna do with your tank. If you wanna have it for practical use, I hope, that you keep in mind the gas, the fuel capacity that you want, location of the petcock, where that's gonna go. The left side, the right side, behind. There's actually, we were talking the other day about replicating a Jesse James footscale tank.
And that petcock, and you can measure that all out. So at the end of the day, you put all the hard work in and it's gone. So the vents, the bung, petcock, the toe, and also there's a few areas that you want to keep in mind on the design. And then lastly when you're done with your tanks, all you do is line them and that prevents any rust build out and also helps sealing it, in some cases. And then wanna leak down test and also do a pressure test and make sure you're not gonna be leaking any fuel or you're not gonna be any gauge on yourself with that.
So that's pretty much all the talking I'm gonna really get to with you guys on that. And with the video, seeing me building this with you, and go through that process, so. I want to start with this when building these tanks. I take with the plywood, I'll take this kind of material and I'll map out the gas tank directly on here. So this might be a little bit hard to see.
Let's map out in pencil here, but this is a top piece for a tank. We're starting down here, all the way through coming up to this point and obviously making the same event for writing on the other side. What you get is making your tank, you measure the end of the backbone where you're gonna stop it all the way to the front towards the triple frames. And taking into consideration that gap in that clearance with your handlebars in it. This is good because once we cut it out, we can actually hold it up to this.
And also if you're gonna make a buck or a reference or a model out of this, you can cut the wood and just put it directly on here and you have it for future reference as well. So if you're gonna continue to build tanks and you think it's a pretty sweet thing, pretty popular, we're gonna go with that. So this is what I use. We used to work, we just start banging away and see what we come up with at the end of the day. You can also use cardboard.
When you get parts or you get anything in the mail, keep that cardboard around. For instance, with this cardboard, we use to reference and contour the outside just to map things out. It's a good part, we've just outlined right here. For like maybe a certain area, in terms of the radius. Map that right out on the sheet metal and you're good to go.
So keep this cardboard around and definitely use that to your advantage here. All right, let's get into the jigsaw. All right guys, it's like 100 degrees back here. So I gotta drink once in a while. Oh, the last piece, I didn't show you!
These are the tunnels. I feel like many of you already know that on your tank, you have a tunnel right there. This goes right directly on the backbone. And when you're modeling your tanks, this side, you can see right here, goes into the mouth or even up here. You wanna make sure there's rubber isolators in there.
Anything holding fluid on your bike, your oil tank, your gas tank, you wanna have some kind of isolator to give all that load, all the bumps in the road and everything so you don't get stress fractures, you don't start to weaken that metal and down the road you have issues with it. You can either make those and you can also buy the tunnels as well, so if you're going off and starting with it, maybe buy the tunnel and then working the outside of the tank would be a good option for you. And then these will be, these are actually mounts, slugs to go on the bottom of the tank. So when you're done building the tank, you're gonna see a mount directly off the backbone. Two of those, put those right in your tank.
Cut out the slots for them, recess them in, and then weld these in and you're good to go. These are also a nice little, stick a quarter on. So check those out. All right. So let's adjust the camera real quick.
Bring you guys in a little closer. All right, that should be better. Sorry about that guys, hopefully that's better for you. All right, so we're gonna start with, like I mentioned earlier, 18-gauge metal. We've got big old sheets.
When you're purchasing metal, the first thing I always recommend doing is taking the film off. On metal, even from Menard's, Home Depot, you'll see somewhat of a slick or a shiny coating on top of it. That's a film or oil that they put on there for a preventative of rust. This one, you can see, has been out there a little bit. But we're gonna take this, grind it down.
And then we're gonna make our outline of the top of the tank. And from there, we'll cut it out and start working on the metal altogether. So I've just got a gentle grinder here. And while we're doing this, what we wanna be careful of with any kind of sanding, abrasive that we're putting on, or if you're using an air tool, some of them are sitting back there. You never wanna go directly on the metal.
You'll see when we go into doing the contours and taking that metal down, what you're doing is putting a dead spot directly in the metal so you wanna go in a circular pattern all the way through and make sure you have an even grinding area for it. That's a little weak, that one's a little weak. So we'll start out with the outline for it. What we're gonna be doing is we're gonna be making that 21 inch backbone. And what I mean by that is from the top of the gas tank all the way down to the rear.
You can see, we're gonna have it 21 inches in length. We're gonna have 12 inches wide on the top piece and then also 12 inches high when we get to the side pieces throughout. And pretty much gonna be reciprocated and be building a Bristol tank, Jesse James-style Bristol tank. So first thing I like to do when doing these tanks, I take some filler rod from TIG welding. If you don't have this, you can use string, electrical tape.
All I'm gonna do is, I'm gonna start getting a contour of liquids. I'm gonna use this for the outline on the backbone and then trace this out. I'll tape the bow and then we can actually just flip it over for the other side. I'll start with that. We have quite a large initial piece to it.
So you're just gonna continue to work the filler rod or electrical tape and get that basic design down. Don't worry about it if you have too much up here. Just trace it out here if you need it. And then take some electrical tape, get the bottom end taped down, and then we'll work off the top. All right, put these on both sides.
So after that point, if you like your design and like where you're going with it, trace that out, but what we're actually gonna do is cut about a half inch extra metal on the outside of this. One thing to keep in mind when you're building your tanks is that as you're stretching or streaking the metal, you're taking away or adding metal to that piece as well. So when we're gonna be working on that top piece, we're gonna need to stretch the metal with a shrinker and stretcher. And also the English wheel does that as well. Pull that metal a little bit farther.
So we're gonna gain metal as we go, and I always like to take away metal rather than adding to it. So we'll add, like I said, half an inch of metal to the outside of this and work it from there. And I'm not too thrilled about this one. Make this one a little bit better. Far better, okay.
So all you gotta do now is flip it back over. You already have your contour, pretty much right there, so trace that other side out. And if it's not perfect, don't worry about it. When you're starting to work the metal, you'll see that it's not gonna be entirely on point, so... I'll show you this, I'm done marking it.
All we're gonna do is, I said 21 inches on line. So I like to do this afterwards rather than starting it because now we have the basic top end piece that we want, we're gonna mark off the top of that piece, 21. And then I'm gonna do another inch on the back for when we bring those corners down and attach them to the side pieces. So we'll go right off that. So what we've got right now.
We've got a basic outline to the top of the tank that we're gonna build. Now I understand, when I first started, it's very hard to visualize a finished tank like that from a flat piece of sheet metal. As you go along and continue to honing your craft here and work with the metal that you'll start to see where the metal's gonna go and be able to design the future ones, maybe, or even the side pieces a little bit better. So don't feel discouraged if you're trying to bang your head against this saying, "Why can't I see it?" It's often tossed well, it comes together. So at this point, we're going to drill.
Add that half inch all the way through roughly. Again, don't worry about being precise right now on that measurement, the only one you wanna be on target with is your backbone though. On adding that inch to it. Ah, I just worked my way around. Adding a half inch to all there is around this.
And then what we're gonna do is connect those all and then cut those, cut this out. It's pretty cool, after this point, when you start to get this cut out, it's a little bit easier to start seeing that tank. All right, so we've got all our markings to add that half inch to the outside. And it's fairly, enough fairly often and then I can get this pretty close. And a little bit all over, just sand those, just sand those edges down.
Now we've got our addition to the outside of the tank right here, all the way around. So a few options if you deal with cutting your metal. I don't neccesarily recommend using shears, hand shears at this point. You can use a side cutter as I'll be using. You can use a Beverly shear that would really cut through this nicely, or even an electric shear, so.
With that in mind, I'll get suited up to cut the metal here. All right, we're gonna cut this thing out. Here we go. And what you can see I'm doing, the first time I'm taking through is I'm marking, scoring up that line all the way through so you have have somewhat of a divot or an indentation that we can take the wheel through and start obviously better after that cut here. All right, almost there.
One thing about working with metal and all these tools is to make sure your safety is in consideration and also stay away from the sparks as much. You don't wanna be right in front of here with the tools where it's coming right at you. You'll have a nice little friendly reminder in your stomach that you're too close. So keep it at a distance, make sure the cord's out of the way as well. One more quarter and we'll be good to go.
All right, tab end, boy. You can see that I continue to stop and just check where I'm cutting. I don't wanna run over and cut directly into the metal cap. all right, there it is. That's our general shape.
This'll be the general shape that we're using. So at this point, we're gonna do what I was starting to do earlier. We're grinding down to get a film off. We're gonna do that, and then we're also gonna deburr these sides so when we're working on it and about to lay in some of the contour that we wanna have, that we're not scraping our hands and starting to rough them up on here. So again, making sure the work surface is clean and you're not worrying about any of the safety precautions.
So all right, it's still right there, so that's perfect. Now we're just gonna take down the cords and start working on working the metal, the fun stuff. All right, let's put these things away. All right, so now what we've got, we've gotta be a nice smooth surface on the outside. Readjust and make sure your measurements line back up.
I know we want a 12 inch width on the major, and we're still right there at 12 inches. So major point right here should be 12 inches. All right, so with the top piece, so this is what we're gonna be doing in terms of designing the top. We're gonna start, we'll make sure we have enough room here on the sides to bring all the connecting right to the outside pieces. So the top, we're gonna have ourselves a little dome at the top and front to pitch it up.
So we're gonna start here. When working with the metal, I recommend just drawing a small outline of where you wanna put your marks and start working the metal over. So what we'll do is after we trace out right around here, and we'll start working the top piece before the bottom half and make our scores right here. And you'll start to see the metal start to take shape, and that's when we'll start going through some of these fun tools. And you'll notice that I'm keeping that line away from the outside because the outsides will automatically start to come in and pull in and then that's where we'll take the shrinker and shrink the metal back up and get it out on the wave form, which you'll see.
And then that's much easier to work with. So I'll always do 'em in quadrants in this area. Not the best job, but it'll be a finished product. So this will start working right here in the middle section and work our way outwards with scoring the metal. And again, this is gonna help stretch it and put that contour right in there.
All right, so I'm gonna hold this with my wood handled piece. Make sure this is spread out a little bit. I'm gonna use the large embossing mallet here and start getting our larger scores. Don't feel like you're putting too much pressure on here. Not as hard as you possibly can and start getting, get those marks in.
Just by doing that, you can start, hopefully you can start to see the radius of this change. All I'm doing is putting those marks in. It's starting to help form the metal. So I like to tell people, just work with the metal, not against it. So if the metal is starting to turn that way, start putting some chops around the outside.
That'll help bring it in a bit. Now you're able to see a lot better how much that actually starts to turn the metal like this. So all I'm doing is still putting those marks in. We're gonna do a couple more. I'm gonna roll it through the English wheel and then we're getting short on time.
So I'll put it through the English wheel and then we'll start working it with the anvil, but... Now for the most part, I know this is gonna be really difficult to see. But this whole area right here is now full of these shots. So we're starting to get a back end area and we need to smooth that out. So the next step, when you're done putting all these marks into place, for instance right here, you're gonna take it through the English wheel and start rotating it through.
And it'll help us smooth out all these bumps. Now with the English wheel, we have different sized anvils. What I have on there right now is, we refer to it as the crown, which is the radius on the actual anvils. This is a little bit more narrow crown to it. This one's nearly flat, and then we have a flat piece.
The reason for that is, it's up in the wheel, it puts more of a radius into the metal or to smooth out what we've already done and get that also without putting in additional radius. So when working with the English wheel, get that out of the way. What Zack would recommend is not getting your fingers caught in here, it does not feel well. So we're gonna take the bottom anvil, loosen it up so the top wheel is not flush with it. You work in quarter inch, quarter term increments with this for your tension.
Once you're done with that, put on your top wheel. Get the bottom wheel going too with it. I'll shoot some WD on here. Got a better, slicker surface. Again, I'm gonna take the top wheel, put it through.
Take that piece, get it in there. Additional quarter turn, and then work with the English wheel. I always put my fingers out to the side. I've got it partway into the side with it. So take it out and work it through.
As you do this, and if you try this, you're gonna see that all of these bumps, you'll feel them go through. Or you'll apply pressure consistently all the way through. Those bumps that'll come out and look good. Get that way. We'll do them, then realigning it.
And right here. And then get to the top piece. We're gonna continue to work our way all the way through. And see no more bumps. And even when we don't have any of our slurry marks in here, we're gonna start working at it at the edge as well.
And so go around the initial marks that we made with our contour, push it back in as well. So from this point... You can see how that really took a turn, literally, with the contour. It's a little bit wavy up in front here. But we'll get that removed with the shrinker and stretcher.
And now this almost scoring marks are nearly all the way up, a few more. So how are you doing this, constructing scoring marks? By going back and forth with the English wheel and the mallet, so it's a combination of doing both. This may take half an hour, it may take a couple hours. But we're just gonna keep working it through.
And so starting with the middle piece, now we're gonna go around these corners, take it through the English wheel, and then bring down our outside of our top tank here. And again, that's where we wanna go with the tank. We're doing that physical style where it's gonna come up and then come farther back. So if you didn't want to have this much of a radius and need to draw it back a little bit, it's fairly easy to start adjusting. What you're gonna do is take these corners that are flared out on you right here and put it through the stretcher.
And that'll cause the metal to expand and allow more metal in here to free up. So it'll start pulling back a little bit. Work your way around on the stretcher and that will help take away that issue that you may run into, but... But see now, it's gonna look like a Caldwell. We'll go back in, eventually we'll take down the materials on the sides.
So only a couple more in here with the small embossing mallet on the corners. And then we'll take it through the English wheel again here. And I'm trying to get now, but this metal is working with us good, I'm trying to get the ripple corner to the waves here so you can put it through the shrinker. So I'll do a few more and then we'll take it through the English wheel and then go straight to the, going down the sides. What I'm doing is I'm focusing on one area of the sheet metal right now.
Because looking at it, it looks like a seat pan that way. But this area on the tank is actually driven down a little bit more than this one. So we're working on this area to drop it back down and we can go through the English wheel. That has helped a little bit. Maybe a little bit more on this side.
Now it's starting. You see how it's a little bit uneven? We can work that out right now on the English wheel. Again, back it out, slope the top wheel. Bring up the bottom wheel so it's barely touching so it can feed right through.
A quarter turn, tighten it up. Let's start working the metal all the way through again. Back and forth motion. It's typically good to keep a back and forth motion rather than side to side, back and forth. Hopefully all the metal.
I like the other side of it, but I'll go in the same direction hypothetically. After it's realigned, you can stress your piece and coming back over. Now it's starting to get a good bend on its side. To adjust that, you see that big bend now? How it's starting to become uneven?
That means this side is a little bit... We need to shrink this side up, pull the stretcher on this side to even it out. So this piece of equipment is the shrinker and stretcher. Like I said before, it shrinks the metal to help bring it closer together. And then the stretcher helps separate the metal as well.
So we're gonna start, all you wanna do is stick the metal into the jaws. Then you're gonna press down on the pedal as hard as you can and work your way around, work your way around the piece here. But remember I said, we're gonna start shrinking this side and stretching this side. And this could take some time to do. You start to think, a big think here.
And all we're doing is going half inch, quarter inch at a time, somewhere in that vein. If you're doing all right. Pretty neat to let it go. That's starting to pull the metal down now, so it'll even out that metal here on the side. With the shrinker and stretcher also, you can start getting some jaw marks and some scarring into the metal.
So when we're done doing the whole shrinker and stretcher in here, you'll bring down the sides so they're flush in. But you'll have to grind them and get that flush. Smooth metal. Just keep working our way around. Believe it or not, put about an hour or two hours into doing this, and you should have something near completion.
Now I'm just focusing on one area now, because I can start to see the metal come back. But if this will start pulling that metal down on this side, and then we'll work to the other side if needed still. It's starting to come down a little bit better for us right here, where all those stretching marks. Now we'll go on and stretch that side. And like I said early on, it's just about being patient with this.
All right, come on now, there you go. Now we're gonna stretch this side, and start pulling the metal apart. We'll work that area as well. You wanna good look out, metal handles this perfect way. All right.
So now we're starting to come down more. Now in this area, what I'd recommend doing, since we have a little bit of a higher radius on this side, put some more shots in here and start working with the English wheel again left to right. And that'll help even it out a little bit, even it out a little bit here. So just look at the metal, figure out where you need to work with, and continue to go back and forth. If it's, you need to put shots in there, take it with the English wheel another run, that's gonna be the hardest portion of building the tank and tapping that out.
So I'll make sure I get to some of these questions for you guys. I'm gonna run it one more time through, then I'll get to these questions. But that's it, that's what you're doing with metalworking. Uh-oh! Take it all the way back out, through it.
Roll it again. So like I said, we're gonna work left to right on here. And that's gonna help with our radius. You can also put a different die in the bottom. That would flatten it out, flatten it out a little bit and bring that arc in a little bit more.
But this specifically, we don't have that. Like I said, we'll pull it back on these. You can see it's already starting to take shape, so... So with metalworking, for everyone, sorry it's getting hot back there now. That's primarily it, this is gonna be the back piece.
We're gonna turn these corners down and make our side piece come up and start working that metal. All you gotta do is really take the time. So making gas tanks, like I've said before is not, don't be intimidated by doing it. Be patient, walk through your design. Lay it out, if you're not happy with where you're at with it or it doesn't work, start it over or the piece is not salvageable, then do something different.
So take the time to weigh that out. And we'll continue to work on this piece as well as the the polar pieces in the near future. All right, we have a few questions that I wanna get to here. Sorry guys. So we have, I'll get to one of these questions.
Putting sports fuel tank, I'm making one, oh you've got two sports fuel tanks. Putting one together with that from the raise from the front 1 1/2. And the back of the seat would be one inch. And you're going from approximately six, you're going to approximately six gallons instead of four and a half. Your question is regarding the welding process.
So you could take it two ways. Take one, it could be a little bit more experience for some people and maybe sometimes easier. If you're going to be welding the pieces together, just make sure you have enough metal. If you're not putting the filler in there, take that into consideration. But TIG welding is the best way to go.
I always recommend putting tacks all the way through, make sure your surface is even. And then don't do a full bead just yet, but take your time, make those tack marks. And that will help smooth any of the metal. And then you can lay your full beads after everything is tacked together. If you're going from halves, I think you are here.
Take a piece of, take your chisel, raise the metal up so it's flush, and start making your tacks all the way through it. Readjust, make your tacks, and then that would be the best way to go without having to worry about, like I said, distorting the metal. If you don't have a TIG welder, lot of you don't have TIG welders. You can also use a MIG welder. Wire feed welder, and make your marks directly on there and doing that.
And you'll have to spend a little bit more time grinding away but that's still the same on the dome. So afterwards, if you're done doing that, like I told you earlier, go through and do the pressure test. Make sure you line it correctly so you don't get rust buildup inside of the tank. And then do a leak down test and make sure nothing's leaking. So it's that part of putting it all together should be fairly simple as far as welding.
Just make those tacks and you should be good to go. I wanna thank everyone for joining us today on this first part of making a pretty neat gas tank. And we're gonna continue to work on this piece. I'd like to do some additional metalworking and a couple of those as well. So remember, when you're working on metal, take your time, be patient, and most importantly, have fun doing it.
So batten up and just enjoy the whole process. And lastly, don't forget to check out the Ready to Ride Sweepstakes and hit that subscribe button and get yourself in store for some sweet parts by Auto Design. Thanks again everyone, and have a great weekend.
Share tips, start a discussion or ask other students a question. If you have a question for an expert, please click here.
Already a member? Sign in
No Responses to “FMH LIVE: How To Fabricate a Gas Tank Part 1”