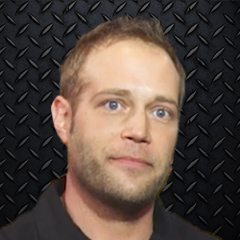
FMH LIVE: How To Fabricate a Gas Tank Part 2
Tommy CrealTommy ‘Clutch’ Creal hosts Part 2 of fabricating a motorcycle gas tank. Dive into the fabrication process with one of the most unique parts on a motorcycle, a custom gas tank. Tommy finishes up the custom gas tank from Part 1 with insider tips and tricks along the way. Tommy covers metal forming, blending seems, welding. Watch now to see the finished product come to surface.
,- All right thanks. Hey guys, Welcome to our August Fixed my hog event. As many of you know me, I'm Tommy Clutch Creal, with High Compression Garage and Chopper College. We're gonna be kind of, running through part two of the gas tank build out that we started last week with a few, more tips and tricks for all you guys. And, I'll run through that.
But, before I get into things, as always make sure you check out the banner, there's a PDF you can download for the fall apparel that's going on with fix my hog. And, it's obviously some good stuff still. So, make sure to check that out. To start things off, and just to recap what we did in the part one. We were, going through the english wheel, showing how that works with the different anvils at the bottom.
We went through some of the, the items with the dollies and how to form metal in the corners. And then, we didn't get into the flashing hammer, but we did use the shrinker and stretcher far back here in the corner. And, use that on the sides to get our contour. So, remember when working with metal in general, you can never really go wrong with it. You can always fix it.
So, last time we were working on the top piece. what we did after that shows we peeled back backwards, and started a different gas tank for you guys. I had an idea this one might be just a tad bit easier to comprehend, and that was gonna be a pretty significant build. So, what we did to kind of get ahead here, is we had this middle part stamped out on the top sheet right here. And work the corners, we gonna work a couple of corners on this, during the segment, and then also finish out the side panels on this tank and weld it in the tunnel.
Now, there's two different types of ways to feed the fuel. It's obviously gravity fed out of these gas tanks. So that's an EFI. You're gonna be putting a different bottom piece on here like you can see right there, or are you gonna be using a petcock. And I'll get to that later on, and where to put it, and how to make sure you're in the right for that.
So that's pretty much. So we're gonna dive into things today, and start with a little bit of, continue to work on this top piece to make sure it forms nicely to here. We're gonna go through a little bit of TIG welding, and weld this tank up for the most part. And, hopefully by the end of it, we'll have a near completed gas tank for us to work with. So, all right.
Let's get into it, let me get my glasses. I mentioned last time, and it's always good to clean the metal before you're doing anything with it. So we're gonna take the grinder and can get some of this rust off. 'Cause it's been sitting around for a few weeks. On these corners, groove down and get these burrs out of here.
And then we're gonna run it through the english wheel to get a better contours to fit. We're gonna be needing some spacing on here. So, we're gonna run it through there again. Just, simple side grinder. You can obviously use air grinders, die grinders, all that kind of stuff.
but I choose to use these electric ones there pretty quick with metal and, you can control it a lot easier of how far in depth you're gonna go down on it. So what we're gonna do, is we're gonna take these sides up real quick. And then, as you can see this piece, we can cut a little bit lopsided right there. So we're around that out, make sure it contours the bottom well. So you can see a little bit better now, These corners are all, all the rust has gone on here.
We're down to pretty much the bare metal. And also with grinding, one big thing that I recommend to people is to consistently go in a circular motion. Rather than just holding the die grinder or an air grinder like this. Go in a circular pattern, that makes sure you don't get flat spots in the metal. And, you don't have to build that up with either welding it back up or a new piece of metal.
So, try to go in a circular motion all the way through, and you're gonna get a better finish at the end as well. All right, so now that we've got the top piece, in better shape than it was. We're gonna move on to the tunnel. Now, when we started, going through and putting these together, I left this bottom portion open, as well as the top portion right here. Just so if we need to split the tank, pull it a little bit farther apart, or bring it in.
We have enough metal to work with here. So, when putting this one on, this back section we have is gonna be a little bit off. So we're gonna have to fill that up with metal. But, as you can see, we're pretty close, right now. And what I typically recommend when building your gas tanks, is to leave the tunnel until the end, unless you're absolutely sure, that top piece is gonna fit on.
So, and the reason being is once you tack weld these on, you're gonna be able to reach through on the bottom with a hammer and dolly, and get that fine contour finish. Unlike if we were to put it on, and you had a big area in here that was flat, you'd have no access to get into that, inside the gas tank. So, it's always, better to kind of leave that area, open. But for the most part, I think we're good. And what I'm checking for right now, you can see a little bit larger on here.
So when we're gonna weld this in and tack it in, we're gonna bring these sides together, side-by-side and lay our tacks down, all around. So, we're not gonna actually want to tack one after another, on this side, because it's gonna contour the metal, and bring that side up. What we'll be doing is placing a tack here a tack on this side and alternating on both sides. So, that'll be key, for us to get going. My partner in crime back there needs to bring the camera up a little bit.
He bring that camera up, just a tad bud so they can see. You could see this bottom portion as well, that we're working on. When I cut in here, we need to fill that all in. So, I typically put another piece of metal add on to these sides. But for today, what we'll do is, we'll lay a couple of tacks down see if we can get that.
It's a pretty significant amount, but, we'll see what we can do. All right, we're gonna be running with the TIG welder. Plug this sucker in. As I mentioned last time, TIG welding is the preferred method to get these tanks all together. Because you get a cleaner weld out of it rather than a MIG welder, but you can MIG weld these.
And there was also a question about braising these tanks. You absolutely can, but obviously, it's a little bit harder, and, different size of talent needed to do that. But it will hold up when you do your pressure test and leak down test with these as well. All right, so what I'm adjusting here on the TIG welder is the amperage coming out. That defines what thickness of metal we're gonna be using.
So, we're more using the 16 gauge metal right here. So, we're gonna lower the amperage and, make sure, we don't actually go right through the metal. So if you're using more of a quarter inch you're gonna jack the amps all the way up, get that thing ready to rock and go that route. All right. I think we're good here.
So, I'm gonna start on the front here. Like I said before, the bottom was already done in here. We actually cut two slices in here for the tabs. But, I'm gonna start right here in the front. Place a couple of tacks and go from there.
Now with TIG welding, you have tungsten at this end. This is where, your pulse is coming out. And unfortunately, you can't use magnets with these, because it will deter the, I'll make your pulse sporadic, all the way through. All right. And then you also want to sharpen these.
When you buy Tungsten, you're gonna see that they're at a flat point. You wanna sharpen these so they're more, have a triangular look or a diamond in the front where it's a very fine point. Otherwise that, it's gonna jump all over. And then, let's get this going. And then filler metals the other point, of TIG welding, you're gonna want to, make sure you're using the right diameter, and the right filler metal for the right application.
So, aluminum obviously has a different kind. and, you don't want to mix those up. 'cause you're not gonna get the results you want. All right, so we're gonna adjust. Adjust my seat in here, so we're comfortable, hold the tungsten out, tighten it up from the back.
I typically recommend using just, about that much, length coming out of the cup here, on the torch. I'm just gonna make sure we're ready to go on this. All right. Now, you see we did a quick tack on there. I'm using a larger gauge filler metal just because of the gap we have.
If it was a flush mount, we can easily just go through it. Sometimes not even needing filler metal. However, this time we do. So, we're gonna go a few more on here, flip this around make sure you're comfortable while you're doing all your welding. The piece is in a good spot, all right.
Take your time while you're welding. All right, another tack, we're gonna do a few more here and then we're gonna work on the top piece and get that in place. All right, one more. All right, so now we've got three on there. I'm actually clean this one up just a little bit.
When you hear that jumping that means, your arcing. Perfect. All right, so now in the front, what we have, we've got three, simple tacks, four, sorry, one, two, three, four. Now that's gonna make sure that nothing maneuvers or shifts on us, as we start working the top section. What I like to do sometimes, either take a flathead, if we need to pry the edges up on here.
So we can actually move these corners out, and make sure we're getting a flush mount. There we go, I know the fans on me. And work from there. However, as I shown you earlier, now you can see that we have a pretty significant gap. So we're gonna take this piece and shrink the sides down real quick.
Allowing us to, get a better fit. I'm gonna pull the shrinker out here. Be careful that metals hot if your welding. So, it's easy to just go on there and grip. So this was the section that we were having bow out a little bit.
We want to bring it in just a little bit to get flush on there. So we're just gonna work these six inches right here and then we'll measure that side. And this typically is already pretty well fit, if you're welding these side panels in. So, sometimes you'll have to do this extra work towards the end. Just put it in, work at left to right.
And the pressure as well, you can adjust as needed. All right, so now this has come in, just a little bit just where we want it. There you can see now, That area that we just worked on, is getting a better fit right there. So we're in a good place. So we're actually gonna do the rest of that as well.
And bring that in, all the way down this side. Yeah, we're doing this because we want to bring that metal in. If we needed to bring it out we'd use the stretcher on here. All right. You can put it in about half an inch, quarter inch and adjust, work it that way.
I typically just do it about half an inch, and that works just fine. All right, again, we just did all that. Now, it should be fitting a little bit better just by those slight, areas that shrink. Much better. This bottom section is gonna be the only section that we actually have to work out.
So in the beginning like I said, either add more metal on here, but for today we're just gonna even those out and then, work from there. So all right, now that it's fitting a little bit better, do the same thing on this side, we're gonna clean up the sides to make sure we have a nice surface to weld with. And then we can actually make some adjustments as needed with the hammer and dolly from there. So I just wanna do a couple areas in the front. We don't need so much in the back.
So also help your coordination and if you're looking to get in the gym, work with metal. All Right, we're fitting a little bit better now. We can work with that. All right, now we're gonna take it down, with the grinder. And then will start, tacking away.
And you could see that there's a lot of burs over here and indentations, and we'll work with that when we get there. Hopefully that's not too loud in the mic. Alright, Zach, can you grab me one of the, hammers over there? We're gonna take in those corners now. From our marks of shrinking with the jaws, it's gonna, you can, might be able to see now the mallets, but that's all right.
I'll work with that one. That there's, you could see the jaw marks with the lines and streaks going through. So what we're gonna do is we're actually gonna take the dolly on this end, before we get the top on. And get those evened out. So it's not so wavy, it's gonna be a lot more difficult to put it in the english wheel right now.
And then, yeah, you can leave it right there, thanks. And get them all sorted out. So, we'll take that. I'm just gonna use a regular hammer. So we have them up here.
You'll see hammers that have a more of a spiral end to it right here. That's also a shrinking hammer. Where you can use it the same effect as a shrinker, and a stretcher. So, that's another little investment that if you're not looking to spend, some good amount of money on a new shrinker and stretcher, you can just simply do that. And I like to put it on here regardless just so it'll stay stationary for me.
So, all to be done, is just working this through. Even these out. Now, also these have different radius's on them. And you can see this one's a larger radius, and this is a smaller one. Depending on what kind of contour you want to get on these sides.
So, rather than me switching around, all I'm doing right here, is as I'm banging the metal in, I'm actually pulling the dolly out just a little bit, to allow it to get a little bit more of a curve in there. So, we're just gonna work this all the way down. And, we need a little more here. All right, that looks a lot better. It's a lot smoother inside here, rather than being more wavy.
And you may need to keep, continue to do this. It may take half an hour, may take five minutes, may take two hours to get all this stuff done. But it's obviously going back and forth to make sure that metal is a perfect fit where you want it. So in this kind of case, what we'd look, you might have to go back and sand this back down, but we're still good on that end. I'm actually work this corner, a little bit.
And the fun stuff about metal is where you're heading a spot shrinking it. There's gonna be another piece that either bows out or it takes a different shape. So, that's what you have to keep an eye on when, not only just building gas tanks, but also when you're going into even fenders, oil tanks, things like that. It's gonna continue to, not warp necessarily. But it's gonna, just give you a little bit more work to do, for, yeah.
All right, so we're gonna do the same thing on this side. There was a big burr and indentation right here, and same thing back here. So we're just gonna do a couple on that end. Yeah, it's looking not too bad. So you can see it's a little bit more straighter here and following the lines.
So I'm just gonna hit this, to get that bur out of there. all right. Much better, all right. Now, from this back section, when we welded this back piece. Like I said it tweaked and everything.
So, what I'm gonna do, just to make it less of a headache, is I'm gonna take down this part that the high spot on the metal to allow this to slide back and get in position with the rest of the tank. And then from there, what we can do is add some metal in there, or you could redo the top piece towards the end. So, I'm just gonna take that down real quick. And then we can work with it from there. All right, we're making progress.
Here we go. So now here comes the tricky part. Now, when you're using magnets with TIG welding. Like I said, you typically can't do that. So, I'm gonna place one right up here at the front because we're gonna be welding back here in this section just to tack it down.
And then we're gonna pull them off, and then just use it by hand or with that flathead screwdriver just to hold that metal up. So let's check fitment again on this top piece. We're looking pretty darn close on there. And then, yup. I almost have to say that we're gonna have to come in a little bit more, so, we got the top piece working, but you could see that the corners are, a little bit off.
We're gonna be welding it right there. So we'll pull these in, then I'm actually do the top piece and pull those in. And that way we can, try avoiding using that larger piece more. And after working with this we may just have to use the dolly and hammer again. All right.
So It's always a tedious process working with metal. And if you're a beginner and trying to get into it, as in a trade or just a hobbyist or a career, make sure, try not to get too frustrated when with working with it, right off the bat. It does take time, and a lot of patients too, start working with it and get down a nice routine. So don't get too discouraged right off the bat. And I'm just doing, front to back, right to left, to bring these corners in just a little bit more.
I don't want to go too far up, because that front end was, fitting fairly nicely for us. So we can always go back and redo that. So again, these corners, you can see we brought them in just a little bit more. You got more of a contour right in here. It's far better.
All right. All right, all I'm gonna do, get this evened out. And then, we're gonna tack this thing on. All right. Looking pretty good.
Make sure if you guys have questions or anything you drop it in that comment section over there, and, I can try to get to it, by the end of this event for you as well. All right, now we're making progress. Yeah, you could see the only jaws and now that we're gonna make, is just to this right, area right in here. Because it's showing a lot more, space than needed. So make that quick adjustment and then we'll get it out.
All right. Check fitment again. You'll see if you're doing this in your garage or, as a career or in your shop. You're gonna be continuing to go back and forth making minor adjustments on these tanks. But it always makes for an easier round at the end.
So, all right, we're getting there. So now we're gonna do, get this welder ready and tack this thing up. Let get some, magnets. Trust me too. We're gonna see if we can actually pinch some of the back down, rather than using a magnet, off the bat.
And I don't think we're gonna, be able to do that. Out of mid air, I don't know where. This tops really given us a, fun time today. All right. So we're gonna try to get it, as first as we can, top section.
I have to do a lot more metal work to the top, but we're right about that. All right, and then we'll adjust the size as needed after we placed that first. But for the most part, we've got it centered on there and then we'll tweak it work in the way all the way backwards. If you guys are starting to get into metalwork and the other thing is maybe recommend doing a offender or a C pan to start out with vendors are typically pretty easy, just because you're just rolling. Same radius all the way through, and then bending the sides.
Then if you're doing a wide size tire, 253 hundreds those are a lot easier to work on than some of the standard ones with, like a bead running through the top. So I'm gonna actually turn up the heat, just stand up just a little bit, make sure our tungsten is good. And then that's a careful place. Quick tack at the top up here. Another one right here.
If we can without moving too much metal doing right over there as well. Another step, we go. We've got one tack, lay another one over here. And the best approach with this is to tack all the way around your tank, and then you'll do your full bead all the way through. All right, so now we've got this thing looking like Frankenstein up here.
So this is the front so its two tacks or we're gonna eventually have to bring this in when we're tacking the sides. Just so we get that same radio saw all the way through. So we're gonna start tacking all the way around these corners and then we'll start with the sides and bringing those in. And all I'm doing with this magnet is keeping it back here. So this doesn't drop when we can actually get in there.
All right, well, let's hit it up again. All right. Now, the one rotate to the other side. Be careful, take your time when you're welding, because at the end of building your entire gas tank what you're gonna recommended to do, is, do a pressure test to it. So what that is is you're actually sealing all the openings here and running a certain amount of PSI to be around 35 into the tank to make sure there's no major leaks you can use.
So squirt it around. Same thing, kind of as a leak down test right there you're gonna find any obscurities during that time of doing that, all right. So now that we've got a few more up here on the front we're gonna work our way and just do two more right here. And then one more. And then we're gonna start working on these sides.
I'm gonna lose that magnet now 'cause we're doing all right. If you ever see your art jumping while welding what that typically is, is either this is not sharp enough and you need to resharpen it. And bring it down or that you more have a ball, and at there, what you don't want to ball in because your arc is just gonna kind of pop all over the place. You wanna be able to make sure it's precise and right where you need it. So now, we gonna do one more on the side, and then we'll do that last one to work on those.
All right, see that front, we've got those tax in place. And if you see anything where it's not lining up on the front, don't sweat it too much right off the bat. We're gonna actually get in there and make sure we're leveling out the metal as we worked for it. So don't worry too much or at all. All right.
It's looking all right. What do you think Zach? It is hear. So now you can see we have some strong tacks, start bringing that metal over starting to meet here on the side. So we gonna start two on this side rotate to this side and then start bringing the tank in, so all the panels meet together.
You can also do this with MIG welding but you're flying right through it. There's one, I just heard the metal start moving on me. We're not gonna use filler on this. Maybe just a little bit there. You could see those corners now, are a little bit more fluff.
And what we gonna do is do this side real quick. We're gonna need a Flathead after this, or I file. Sure. There you go. Thank you, bud.
The reason for this is now what we've got on this side, is we've got a larger gap than we really want. So this gap right here. So what we typically do is if we're not using flathead I'll use the small file, but bring it over just like that. Now, we have a flush area. And we'll just leave it right in there and tacks it and move your way on down.
And you gonna end up probably doing this quite a bit on your tank. All right. Let me just do one more. We'll move this file for those Flathead. See now, after doing that, that entire corner is now flush, rather than have that lift or that over.
No, I'm good, thanks though. You can start to see the metal, how it's trying to bow on us when we're trying to meet these corners but we're actually gonna get down here and get that taken care of. So we're gonna do a few more on this side, work our way down here. Make sure we don't run out of time with you, get this thing dumped pretty quick. And what's happening is, my tank is actually starting to ball out a little bit.
So that's why you see me popping it like that. All right. Starting to make progress down here. I'm gonna go over to this side. Now we have a lip that's overhanging, right here.
So all we're gonna do is get a, try that out a little bit. So we have some more room. So a little bit. So that works. There we go.
Run this all the way through. All I'm doing is using the existing metal that's on there and melting that. All right. Pretty light, slight tacks. We're just gonna keep going.
If you run into anything where you see a bowing out, now, is the time to kind of hammer those areas out which I will probably do in about five minutes here and show you just in case but that'll help make sure those contours of nice and smooth up there. And then you have a nice finished piece at the end. See the incremental amounts I'm going. I'm gone about every half inch all the way through now, just because we're starting to get to some of these larger gaps where we need to pull the corners. Now, we're starting to get a pretty good fit starting to take a shape.
And if you need to, you can always take a larger vice. This is not a vice grips or the rubber ones, bring them on the sides. Bring it in and that'll get you that, that nice flush connection you're looking for. Now, what I do is, when I do that gets that all flush again. And it's not, you're getting that gap when you bring it all over smaller, flatheads are usually easier.
You can see that that gap is gone and now you have a flush area. Just got to get the stay there for you. All right. We'll do one more. I'm gonna show you the front here.
All right, you can also, so what I did on this one, I'm gonna get up for a minute. I actually left a gap right there. Where's the nozzle? We can still get access to it and actually beat the corner all over. And now they're all taken up Same thing on this side.
We'll take them In a little bit. Now it's starting to take better shape. You could see over here, we're gonna have to do is bring that all over. And then fill that in a little bit. Now, what I'm gonna do is I'm gonna jump ahead real quick because we have only 10 minutes to go and well the front up here, and show you how much it actually tweaks on this side.
If you don't have this fully taxed. So you get a good idea of that. Run into a few questions for you guys that I saw come through and get those tapes, and get those answered for you, all right. Now, start to move for, as a little bit. This point, gas tanks so, get the big old ball end at the end.
He could see that. So the arc is actually jumping all over the place on me right here. So just to follow up with a few more things on your tanks so on your top end, you're gonna need the bung somewhere and just use a simple hole. So insert the size of the bone that you want. And while that, or braise that in whatever you need, there's always gonna be some sort of vent in here.
So make sure you're getting the right gas tank cap for that as well. Usually you're gonna have, if you're doing a split tank, and you're doing two pieces like this, you're gonna have crossovers on the bottom section of this tank. And those typically you wanna make towards either the front or the bottom side. So you're able to get as much gas as possible. Number one, and then number two, that they are clearing anything that you may have on your bike.
If you have, not a stock frame or a chin spoiler or whatever it may be. You just want to take a caution into that. Additionally, with the petcock or EFI depending on what you're using, if you are mounting this on, say Jesse James Diablo, type of frame, you can obviously put a fresco style. Petcock back here, shoot it out this way, drop one on the side. You'll see it a lot with more of the stock applications that they're directly right here on the left side of the bike, and run into the the carburetor on the right, but not necessarily needed.
So you can obviously put it on the right side. The only word of caution that I tell you guys is that to make sure when you're putting that, that you have enough clearance for any aftermarket items that you may be putting on, or anything in the future that you might change up. So if it's just a temporary kind of thing then obviously just put it where it's needed or where you feel. It looks the best and cosmetically and go for it with that. And then the last part is your tunnel.
So on the bottom of here, you have your tunnel going through and you can form your tunnel pretty easily. We're making two halves of a gas tank like this and a top piece. You can take the same diameter tubing that you used or have on your bike. And use some oxyacetylene heat that up, bend it over just a piece of same diameter tubing and get that tunnel, and then you can flatten it out with a sheet metal break or even there at your garage. Just simply put it right in there.
And boom, you're done with that, and put it right on up. Keep in mind that with the tunnels too, it will take depending on how big or large it is that will take away from your gallons. If you're looking for a 2.5, three gallon sized tank it's not too significant, but something to consider along the way. And then also the clearance side of things you wanna make sure, up to par as well. So if you're make it steeper at one end and make sure it slides up the backbone and has a big kick out in the front like that first part, one of the the gas tank that I was showing you guys how to do the top piece, that one will really kick out.
So keep in mind that it's something to keep in the back of your mind. There's a lot of moving pieces and considerations with making gas tanks. And a lot of patients, you run into stuff like this, where the middle splits and it's not forming together, and you may have to go back, and make a whole new backend piece, cut it right here and extend it all. You don't necessarily have to make the whole thing. But the good part about metal is you can either take away or add as much as you want, where it's needed.
And then you're good to go. The last piece of advice I can give you for today is if you're running into problems with your side areas or your top piece, maybe consider just doing two half pieces. That's how I first got into building gas tank. I did two half pieces and I must've gone through. I don't know, five A minute and I could actually use, so bend your front end, using English Wheel, get that contour down.
And you even can fold over the top with that and then wait until the end to do the tunnel. So if you run into anything like this, or even on the top, you can still get your hammer, a Dolly in there. And if possible, run it through the English Wheel with a very low size crown. So you're not using an anvil like that size, but completely flat, and you can run it through that way. And it also opens up some options to design wise too, with those as well.
And then the other thing with the tunnels on the mounting points, that's the last thing I want to talk with you guys about, is that, either you see a lot of tanks out there, that have mounting areas right appear in front, tangents or tabs that come out, and then also something potentially in the back, and the reason is just preference. But when mounting your gas tanks, you could even put blocks in the bottom here, and have a directly under your backbone mounted there. Nowadays, with a lot of these road glides, or street glides. more you do is two tabs in the front slide right in and bolt the back and bolt or sorry, bolt in the front and then a bolt in the back. And it's pretty simple, but if you're kind of going for a customized look into things, it's not a bad idea sometimes to explore with different mounting points.
But make sure you do use a rubber isolate or grommet and that helps prevent any cracks or infractions that could happen to your tank along the the road and for the viability and strength of it. So those are the big things with doing that. Additionally, that's pretty much the nuts, and bolts of building gas tanks. Like I said, try running through with a fender. And that would probably be a good start to get used to the different kinds of metals, the gauges, how they form, and also get a good use of the tools.
So there's a, you don't need top of the line, bead rollers, and in English wheels, and turn presses and things like that, or power hammers. And you can simply make one out of your garage by gonna your local hardware store, and just get in a few hand tools and start in that way. But it is, it's a fun adventure. So we did have a couple of questions. I think I got to most of them in the video, or this event here but, someone did ask about brazing their gas tank.
And that is definitely a possibility you can do that. There's no really downsides to it, unless there are gonna be leaks or anything. But if you're capable of doing that, you could definitely do that. I see a lot of people doing their bungs brazing and then obviously their vents on the bottoms are sometimes braised. So that's doable.
And then also we had someone ask about modifying the existing gas tank that you do have. And with that, I gotta get this thing off. With modifying your existing gas tank, rather than opening your entire gas tank up. I tell people to try just doing a dummy section out, in unless you're trying to go for additional gas capacity, fuel capacity, or if it's just cosmetic we'd done tanks in the past with the left side's gas and the right side holds, all the gauges in the and the electronics. So you can just simply put metal over the sheet metal around and work off that, or even add materials on the side.
So that's, that's always a good and fun step is taking the existing tank, and kind of rolling with it from there and making your adjustments if you're just getting into it. So if you have any questions going forward with this kind of stuff, make sure you let us know in the comments section, or on a fixed my hog.com and we can get to those and be have any ideas for future videos or want to know about more fabrication items or go more in depth. Let us know about that too. So have fun, get in the garage and start building that gas tank and as always been a pleasure. Thanks guys.
Share tips, start a discussion or ask other students a question. If you have a question for an expert, please click here.
Already a member? Sign in
No Responses to “FMH LIVE: How To Fabricate a Gas Tank Part 2”