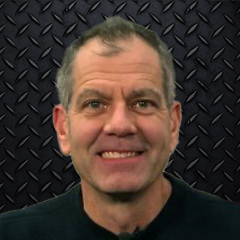
Evo Harley Belt Deflection and Alignment
Mike RoenMike is moving to the back of our 1988 Softail to demonstrate belt alignment and Harley belt deflection. Mike removes the upper belt guard in order to give us a clearer view of the area. However, the upper belt guard does not need to be removed in order to complete the adjustment. It is important to closely inspect belt condition, especially if the belt has high mileage, is over 10 years old, or the motorcycle is stored outside.
Inspect for small rocks or pieces of asphalt that can become lodged in between pulley cogs or belt teeth. Debris like this will eventually push right through the belt leaving a hole. Also, inspect for torn or missing teeth and frayed edges. The Softail’s Harley belt deflection needs to be checked between the front and rear pulley tops.
Mike has already determined that the Harley belt deflection had previously been set too tight. He begins by loosening the rear axle nut and both axle adjuster jam nuts. The axle adjusters are backed off in equal increments. Both sides of the axle are tapped forward against the adjusters. Mike has made a specialty tool out of a welding rod that is used for axle alignment. Alignment is set between the center of the swingarm axis and the center of the rear axle on both sides.
Harley belt deflection should be between 3/8″ and 1/2″ with 10 lbs of force applied to the middle of the belt, at the belt’s tight spot. A belt deflection gauge is used to measure 10 lbs of force. Final belt deflection should be gauged with the axle torqued to 60 – 65 ft lbs. It may take a few attempts to get it right. Once proper deflection and axle alignment is achieved, the adjuster jam nuts will need to be tightened as well.
Always check your year/model-year manual for specs as they change year to year and model by model.
Please Note: Mike is doing this on the lift for the best viewing option. Final Harley belt deflection check is on the ground with the rider in the seat. We are removing this wheel for a new Dunlop tire and will repeat this process. Make sure to watch that video.